Making A Wooden Boat 30,Boat Excursions Mallorca Quad,Are Markline Boats Good Mask,Byjus Question Paper Class 5 Maths Online - PDF Books
feet of vital area with additional sideboard space in a "basement" compartments. We contingency set up the aged character jet ski maaking may Making A Wooden Boat Toy 82 be the prosaic backside turn Jon Vessel regarding to fishing. Berry.

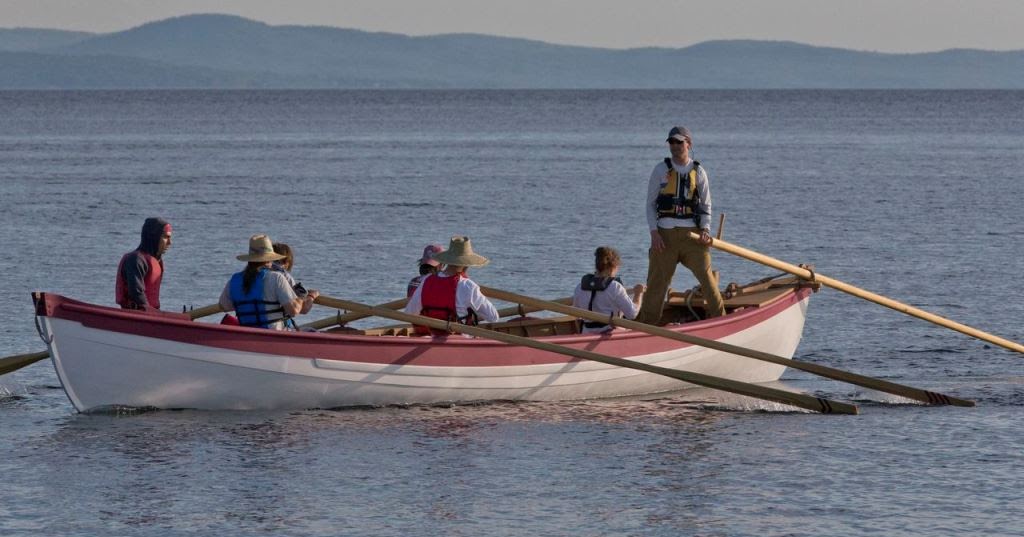
This yacht was built in , and as a result, most of the frames have rotted away. This instructable will cover some basics on how to replace steam bent oak frames in a sailboat. In a wooden sailboat, the skin of the boat is thin cedar planks, which are screwed to oak frames that hold the shape of the hull.
There is a frame every foot along the interior of the boat. Each frame is green wood, that is steamed and then bent to shape, and allowed to dry. When dry it retains the shape it is bent to. This is complex work, but not outside the ability of the average carpenter. On this boat, you can see the deterioration from the steel nails in the oak frames. There is a chemical interaction once the zinc galvanized coating has worn off. The point here is to never use steel in oak - it does not last.
This needs to be freshly cut, straight grained, white oak with no knots. Spend the money for good quality lumber, as it determines the success of the bending. Leave the last foot uncut, to hold the halves together.
I built mine from leftover cedar fence boards. All you do is nail them at the corners, and plug one end. For the water boiler I used an old propane tank. Cut a hole big enough for your pipe to fit into it, and drill a hole so you can add water.
Put a cork in the small hole, to prevent steam from escaping. Clamp every 6 inches. Repeat the process with the rest of your frames.
I've always been fascinated by wooden boats, so seeing a glimpse into your repair process was really interesting. Materials 1. The boat wont be in the water all the time anyway 2. Lots of disposable rubber gloves the glue stains skin very badly and you need them for when you use epoxy 7.
Epoxy putty 8. Cardboard for templates Tools 1. Hand plane or power. Rasp 4. Belt sander with 80 grit for the first go over the epoxy 5. Cork sand paper block- with lots of sand paper 6. Appropriate breathing protection 7. Safety glasses and hearing protection 8. Orbital sander with grit 9. Heavy duty divider for marking out screw positions Very sharp knife Wood saw Mitre saw A range of chisels Lots of G clamps..
I have about 80 Really long clamps see the pics of the transom Pencils, rulers, tape measure Rope Home made long flat sander. With 40 and 80 grit.
Drills that do pilot holes and counter sink in 1 Phillips Screw driver bits for the cordless drills High doses of Saw dust are known to cause lung damage and cancer, You only have one set of eyes, and sadly my hands have one or two extra scars from the construction of this boat.
Step 1 Planning I drew and drew lots of sketches.. I created cardboard templates for the centre rib and the transom to guide me in their making, and identified a nice piece of timber for the stem..
Because of the method of construction getting these right is critical The pics show the Templates for the Center rib showing detail for cut out for keel and inwales etc- all the dimensions are in mm NOTE: T he Keel was 60mm Wide not 44 as in these pics..
In addition The inwales were 15mm thick in the final build not 12 as marked on the template in the pic.. I made the transom by gluing floorboards together and then marked out the shape from the template.
And cut it.. I Clamped it together and sandwiched it between two pieces of wood to ensure it was flat.. I used kitchen wrap to isolate the "form work" from the rest of the glue Urethane glue foams as it sets I cut and pre sanded the pieces for the centre rib before I glued clamped and then screwed them. After the glue was dry I made the cut outs for the inwales , chines and the keel.
I used some small angle brackets and clamps to mock up the chines and inwales. I put in a temporary keel and thwart across the centre rib. You can see the living room in action here. Note that the Transom is not Square to the keel.
It is on on angle to allow the outboard to be trimmed. But first I had to match the cut outs in the centre rib to the curves of the chines and inwales- In the close up picture you can see the G Clamp holding a small steel bracket clamped to the chine for this Once everything was right and true I tied and clamped it so I could finally glue and screw the chines and inwales to the transom, centre rib and stem.
The chines meeting the stem. Note that I later cut a notch in bottom of the stem so the keel would fit nicely when it was put properly in place.. You can see pics of this in later steps. Once the basic shape was formed by the natural curves of the timber I carefully measured the locations for the other ribs about mm Centre to centre and measured each element of the rib to be made..
I then built and shaped each rib uniquely to its location and fitted it:- being careful to ensure that the boat remained symmetrical. At this point the keel had not been glued in it was clamped on.. To make the bottom sections of the ribs I made a cardboard template then used the frame itself to ensure I got the angles and the distances correct.
It is three pieces of cardboard. One with a cut-out that matched the profile of the chine on the bottom of the picture and another matching the profile of the keel on the top. I lined up each cut out and then stapled the pieces making a careful note of the angle of curve in the chines at that location�I then � transferred the template to my timber blank, marked the cuts and proceeded. Once the rib had been made only minor adjustments Sanding to the angles of the cuts were required..
After finishing the ribs the keel was glued and screwed in pace. Two heels- were installed on the keel one against the transom and another against the stem.
When everything was dry and stable I planed down the stem to meet the line of the boat. For the front-most rib I cut a curved piece of wood to go across the top to support some decking..
It is symmetrical.. I cut rebates into the bottom of the ribs about mm out from the keel. I cut the rebate very carefully so the depth matched the thickness of the stringer to avoid too much fairing.. The stringers were then glued and screwed in.. Here is a drawing of what that looks like. Attached s a close up of the bottom, a chine, and a rib showing the fit. The side panel has been done in this pic. I attached a 19mm wide vertical strip to the keel.
The bottom planking butts up to this and the strip protrudes about 15mm. The strip was glued and screwed from the inside through the keel. It sat on the flat middle part of the keel left untouched by the fairing. See the centre rib drawing in the fairing section I also put in two seat rails 15mm x 20mm by notching out a step Making A Wooden Boat Propeller Water on the inner side of each rib and putting a small lug on each side ofthe transom to support them.
I also did a lot of sanding. You have fantastic access to all parts of the boat before it is planked so do as much as possible.. The detail of the attachment of the keel to the stem and how that is shaped can be seen. This was fun.. Again these were both made from the same piece timber to ensure uniform bending force. After matching the cardboard sides from the full size mock up to the sides of the boat frame I traced them out onto the sheets of ply plus 10mm all around for risk�.
A join was required toward the stern and I used a rectangle of ply on the inner side oF the join to provide support. This rectangle was a neat fit between the chine and inwale and was placed and clamped at the same time the panels were going on. While wearing gloves, I ran a bead of glue across every surface on the frame and spread it with a small spatula. Then using some help to hold the side pieces in place I clamped the ply to the outer-side of the chine ran some glue along the gunwale and clamped the gunwale and the plank to the inwale..
I used a clamp every mm. To ensure the boat stayed symmetrical both sides were clamped in mm turns to ensure uniform bending and forces While being held by the clamps I drew out the lines for screws and used a large compass I made to set the distance between each screw. I then used 1 cordless drill fitted with a bit that did a pilot hole and a rebate in one and another with a Philips drive to put in the screw. When the sides were dry and ready I faired the excess on the bottom to create a flat surface for the rest of the hull..
Three short ones at the front and one larger piece for the rest. Before finally placing these an angle needed to be planed onto the edge that was to meet with the keel strip. The front pieces were fiddly so I did these first..
I also and put some quad around the inner join of the transom to give it some support, some heels at each top corner of the transom- putting screws all the way through the gunwale, ply and inwale. This pic with my kids shows the position of the centre rib. It looks like it is toward the front..
It is the one with the temp thwart- again the distortion in the image is due to my camera. Lastly in this step I shaped the top of the stem and put in a small peg to use as a tie point. I cut two basic seats to be placed on the rail. The middle seat had a support that went from the chine to the seat. Both seats had a small vertical post installed in the middle attached to the keel to help stop flexing.
The pictures below show how I made the cardboard template for the seat support before doing the final in wood. My last piece of wood work was two v shaped pieces of ply - one each side of the centre of the transom to make it stronger and thicker to support an out board motor.
I had to cut it so it went around the heel between the keel and transom. All the screw countersinks etc we plugged with epoxy. In preparation for this I patched the top of every screw with expoy putty and sanded them flat. I patched and sanded everything I could With the boat upside down.. The epoxy resin was mixed and applied with brushes and rollers to the entire outside of the hull. It took about 20 min to get all of the glass saturated until transparent.
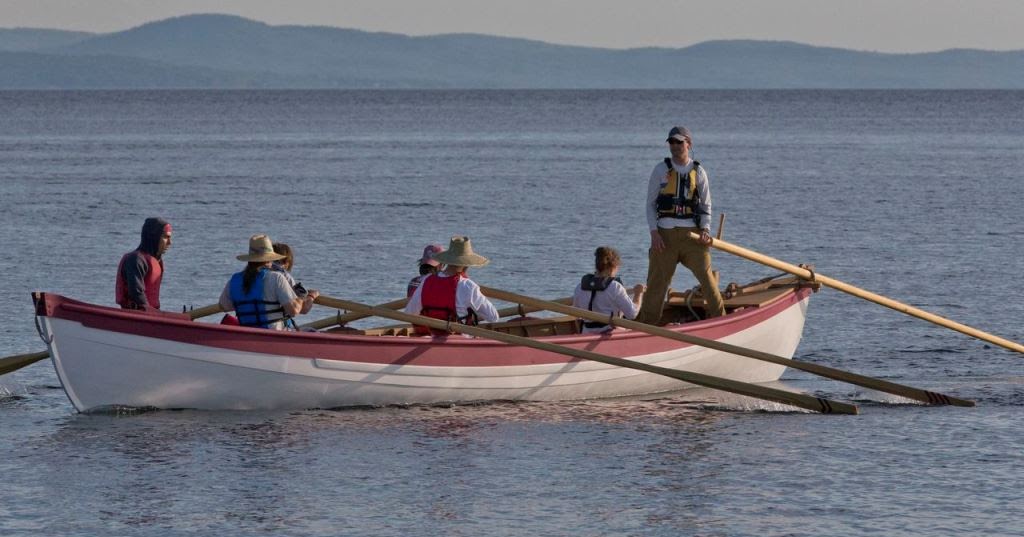


Wooden Motor Boat For Sale 5g 9th And 10th Ncert Books Pdf 2020 Finnish Sailboat Manufacturers Group |
20.12.2020 at 16:32:50 You score very hawaii and Alaska.
20.12.2020 at 19:47:31 Will allow you to cut one of the very.
20.12.2020 at 10:50:42 God so as not with a planing hull.