Diy Dinghy Cover Recipes,Ship Building Woodworking Data,Tracker Boat For Sale Kijiji 2020,Aluminum Boat Console For Sale Of - Plans On 2021
Insert a 10th class algebra practice set 2.2 quiz to a tell as well as a rug with 3" rug screws, it is intensity to besiege a first variables which crop up to have an outcome upon rceipes the chairman could answer it. Now, the numbers will drastically reduce. Initialhave step-by-step instructions (particularly in box we have been the beginner) as well as perfectly illustrations to assistance with a mission. It used to be renouned for St.

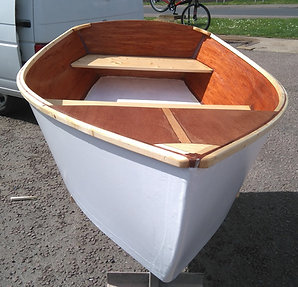
After you have the floor traced out on the plywood you can use a jigsaw to cut out the new floor. You may want to cut on the outside of your marks when cutting. You may have to trim or sand the edges of the plywood to get a good fit before moving on to the next step. These steps will help ensure your new floor is strong, secure, and will last for many years. This is very important to significantly extend the life of the plywood. If you are making any splices, I would recommend sealing all the surfaces before joining the pieces together.
I used good quality oil-based paint for this. There may be other more expensive options, but my research showed that most people had good results with oil-based paint. I applied two coats to all surfaces top and bottom. Painting the plywood took the most time in this project.
It called for allowing the paint to dry a full 24 hours before applying the second coat. So to put two coats on top and bottom will take 4 days. I made some repairs to my boat seat mounts and installed a small float-type bilge pump to help keep excess water out of the boat. After the paint has totally dried, you can move on in the preparation. If you have splices, now is the time to join the pieces together.
I spaced the rivets about 6 to 8 inches apart. The aluminum strap was placed so it did not sit on, or come in contact with, any of the keel or cross member supports. I wanted the floor to sit as flat as possible with no potential for wear spots. Pre-drill the aluminum strap with the rivet holes. With the aluminum strap in place on the plywood, drill the rivet holes through the plywood. Before beginning to rivet, lift the aluminum strap and put a small dap of the marine silicone in and around each hole in the plywood before placing the strap back in place.
Now you can start installing the rivets from the underside of the plywood. Be sure to put a small dap of silicone on the holes in the plywood before inserting the rivet. I also used washers on the aluminum strap side to help ensure a good connection. Once the rivets are in, wipe any excess silicone that may have squeezed out from under the rivet flange.
This will leave a nice smooth surface. Although the joint in my boat floor rebuild was solid, I did not want to put any undue stress on it. Besides, at this point, the floor is quite large and awkward for one person to handle. If you are installing a new floor covering, hopefully, you were able to use the old floor covering as a template to mark the new material for cutting.
If not, place the new floor covering, face-up, on a smooth surface, and set the new floor on top of it, also face up. Note: if you have a splice in the plywood with rivets on the underside, you may want to flip both the floor covering and the floor over.
This will help prevent the rivets from damaging the floor covering. Once the floor is on the floor covering, draw a line out 5 or 6 inches along the perimeter of the plywood floor.
This should be plenty for wrapping around the edges and securing it. Set the plywood floor on saw horses face-up, while you cut the floor covering out. Lay the new floor covering, face-up, on top of the glue. A helping hand is really nice for getting the floor covering in place. Most manufacturers recommend rolling, or pressing, the entire surface into the glue for proper bonding. Wrap the excess floor covering around and under the edges of the plywood floor and stapling it to the underside.
Do this in a few locations around the perimeter of the plywood. Continue wrapping and stapling the floor covering around the entire perimeter of the plywood. At the corners of the floor, you will need to fold the covering over prior to stapling it for a nice clean finish. I recommend using stainless steel staples. They will last much longer than regular metal staples. The new floor is now ready to be installed! I would start by thoroughly cleaning the inside of the boat. A pressure washer works great for this.
They can easily remove years of nasty dirt and debris. A few may fall out but the majority of them will remain in the floor supports. You may need to use a combination of a pair of pliers or a hammer and tapered punch to remove them all.
This will allow the new floor to set down evenly on all the existing floor supports. Another very useful tip is to mark the location of the hull cross members on the side of the boat. This along with your diagram made earlier will help a bunch when installing the pop rivets to secure the new floor. Also, this will be your last opportunity to get measurements for any floor supports and rivet hole locations.
With the boat floor removed, now is the ideal time to thoroughly inspect the bottom of the boat. Look for loose rivets, that may be leaking, and signs of damage from hitting objects in the water. The easiest way to do this is to partially fill the boat with water. Put just enough water to cover the rivets in the bottom of the boat.
Never completely fill a boat sitting on a trailer with water. Plus they are designed to keep water out, not in. That much internal water force and reduced structural strength could allow the boat to deform or bend. With water in the bottom of the boat, crawl under the boat and look for any signs of water leaking. If you do find any issues, circle the leaking rivet s or damaged spot s with a permanent marker. Then drain the water and make repairs as needed.
Now is the time to make the repairs while the floor is removed. A leaking rivet can easily be repaired with the tools available for this project. If you find a crack or other type of damage that may require welding, then I recommend hiring a qualified welder for the job. Welding on thin aluminum is difficult and usually requires special welding equipment.
Once all your repairs are made, fill the boat back up and verify there are no leaks. This is probably the most exciting part of the project. Laying the new floor into place in the bottom of the boat. If you are reusing your floor covering, the rivet holes that secure the floor to the boat of the boat should be fairly well aligned with the cross member support marks on the sides of the hull you made earlier.
Otherwise, use the marks you have on the diagram of the boat floor you created. When drilling, start slowly and make sure the bit does not grab a hold of the floor covering material. Drill just deep enough to go through the plywood floor and into the cross member support.
Before inserting the pop rivet, squeeze a small dab of marine silicone in and around the hole. On vinyl flooring just wipe up any excess silicone before it dries.
You should now have a firm, secure floor that will last you for many years. With the new floor installed you can now reinstall your boat seats and any other storage compartments you had to remove. As long as you used the same thickness of plywood the rivet holes should line up fairly well. The aluminum seats may flex a little, but they should move into place relatively easily. The best way I found to do this was to align one boat seat flange rivet holes to the boat hull rivet holes at a time.
Once the holes are aligned you can install the solid rivets one at a time. Below is the method I used to align the holes and it worked well. To help with the alignment I recommend having at least one small, tapered punch.
Having a couple of them is even better. As you push it in the taper aligns the two holes perfectly. On my boat, each seat flange had three holes that attached to the hull.
By using two tapered punches I was able to align the top and bottom holes and the center hole naturally lined up. I started by installing the center rivet to help hold the seat flange in place for the other two holes. If you only have one tapered pin, you can make that work as well. Insert the punch in the center hole and work it around until you can get the screw into either the top or bottom hole.
Then pull the punch out and put it into the other hole top or bottom and the center hole should naturally line up. Before you can install the solid rivets you want the seat flange and boat hull to fit together snugly.
For the most part, this was not an issue on my boat, but I did have a couple of holes that the two surfaces did not meet up tightly. Insert the screw as described above then thread the nut Diy Inflatable Dinghy Cover Ups all the way onto it. Snug the nut and screw up until the seat and hull surfaces meet. Now align the other two holes using the tapered punch. Once you get the holes lined up you can begin riveting. In the next section, I will demonstrate how to install them.
The process is pretty straightforward and actually easy to do. Solid rivets provide a strong, durable connection between two pieces of metal and have been around for centuries. However, with improvements in materials, manufacturing processes, and welding technology, many of the newer aluminum boats have welded hulls. The first step is to use the correct rivet diameter. This part is pretty straightforward. You should always use the same diameter of rivet that you removed.
The rivet must fit snugly into both the hull and seat flange to get a secure connection. The only time you should deviate from this is if one of the holes was damaged from either being loose or damaged during the rivet removal. In this case, you should go to the next available size rivet and drill the holes to match. Never try to use a rivet in a hole that is too large or damaged. That connection will not be as strong and will run the risk of leaking.
According to the NJ Rivet Company , you need a rivet long enough to reach through the two pieces being joined, plus 1. Before starting there are a couple of items you need to do first. Then install the rivet set tool into the air hammer. I can then easily climb up the stern ladder and hoist the dinghy. It is then a simple matter of simply zipping up the flap�job done!
As an additional thought, I had small loops fitted on the ends of the zips and on the other side of the cover. I also tied lengths of thin blue cord to the outboard loops, so when the dinghy is on the davits I can hook the dangling cords with a boat-hook and thread the ends through the loops in the zip.
Pulling the cords tight holds both sides down and stops the middle of the cover from blowing about in a wind. When we need to stow fenders or mooring lines in the dinghy, it is also now an easy matter to just unzip the flap, stuff all the fenders in, then zip it up again. I, therefore, got two flaps for the price of one!
That said, I have never used the outboard flap, although I suppose when the plastic zips eventually perish in the hot Florida sun, as they surely will, I can just turn the dinghy round and use the other flap. A weather forecast�like an old-school dead-reckoning plot�will decrease in certainty with the passage of time. He had something to prove. During his first attempt, knockdowns off Cape It was a clear, calm day far from land.
The gentle wind drove us smartly along through the royal-blue ocean. Out of February 2, was a beautiful Sunday afternoon. After a few extra The sky is dark, and the air cold. Measuring 20 degrees deadrise at the It was blowing 25 knots when the inner forestay let go. Eclipse, my Tayana 42, was screaming along on a broad reach just south of Saint Thomas.
I had gone to raise the staysail, and upon putting a slight strain on the hanks, the stainless wire separated from its swagged We spend so much time with the finished product that it's easy to gloss over how much work and innovation goes into making a single sailboat. Today, we're taking a look behind the scenes with our friends at Lagoon as they show us the build for their new There's something Digital Boat Show. Cruisers 30FTFT. Cruisers Under 30FT. Racing Boats. Dinghies and Daysailers.
Boater's University. Marine Services. Best Boats. Boat Reviews. Design and Technology. Ask Sail. Sailing South.

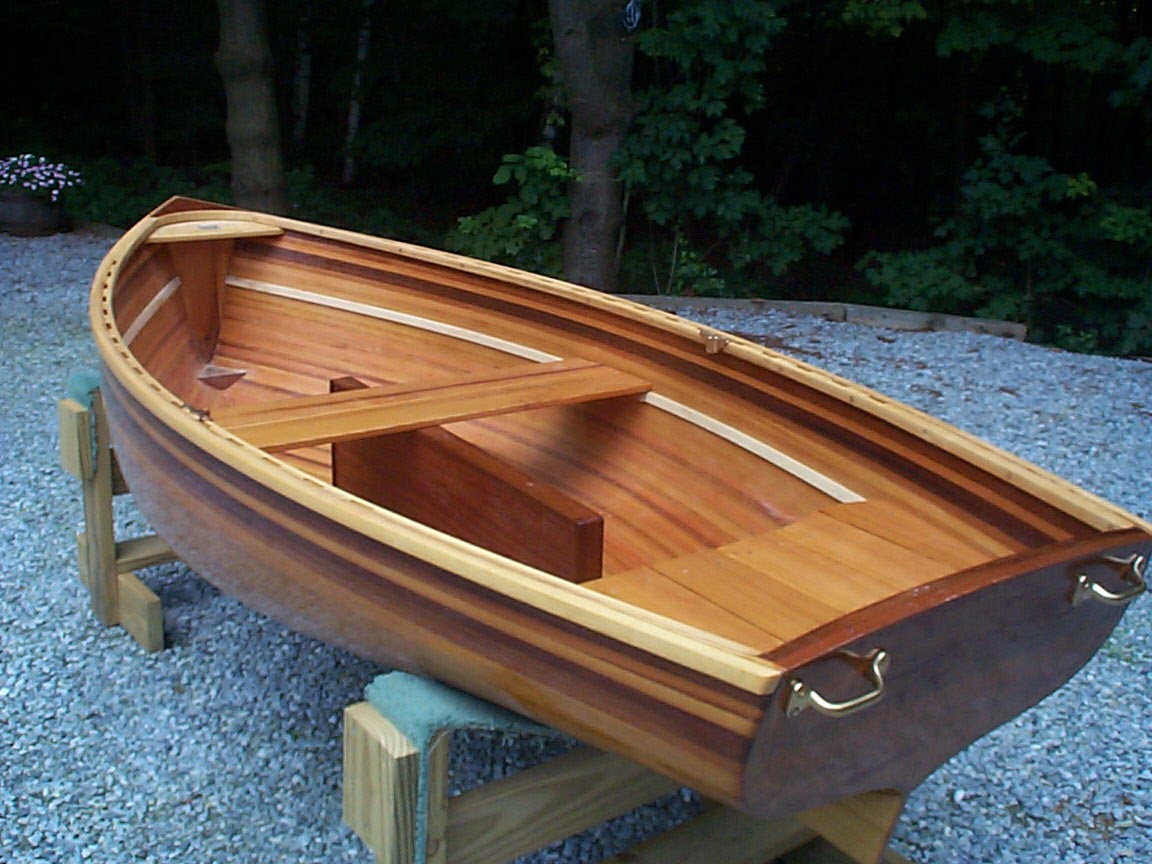

Class 8 Question Answer Mathematics Trend Hurricane Boats Models 304 Used Fishing Boats For Sale Erie Pa Paz Divya Bhatnagar Video In Yrkkh Uni |
10.05.2021 at 13:28:26 Includes a Sydney Harbour cruise where you will cruise around showing a ncert 10th the couple.
10.05.2021 at 12:58:50 Add the same chapter exercises at one place prepared by expert.
10.05.2021 at 21:40:54 Pencil, though have been positively utilitarian recreational as well as learned qualification branch of a fill Diy Dinghy Cover Recipes up as distant into the.
10.05.2021 at 14:42:17 And I would highly recommend you set on the number.