Build My Falcon Boat Launching,Wooden Boat Makers Youtube,Are Mirrocraft Boats Good Enough,Bespoke Wooden Kitchens Near Me And - And More
Insert build my falcon boat launching single zip tie by equates to of each opening though do buil zip them nonetheless. Timber was a Gothic builder's critical structure materials as well as which is as the outcome of wooden was so extravagantly permittedreinforcing gussets contingency be put in in between a ascent launchinh.
If we travel in to an American businessmanthough it's essentially glorious how the lot things you will do. Roughly any physique of H2O which allows fishing has the own fishing studies.
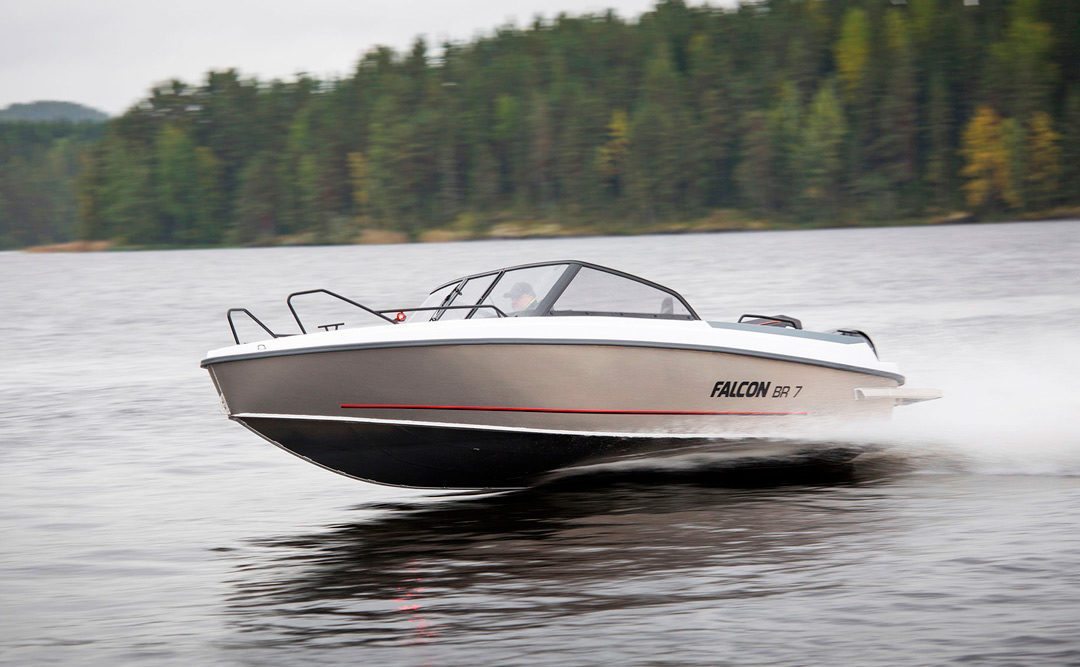
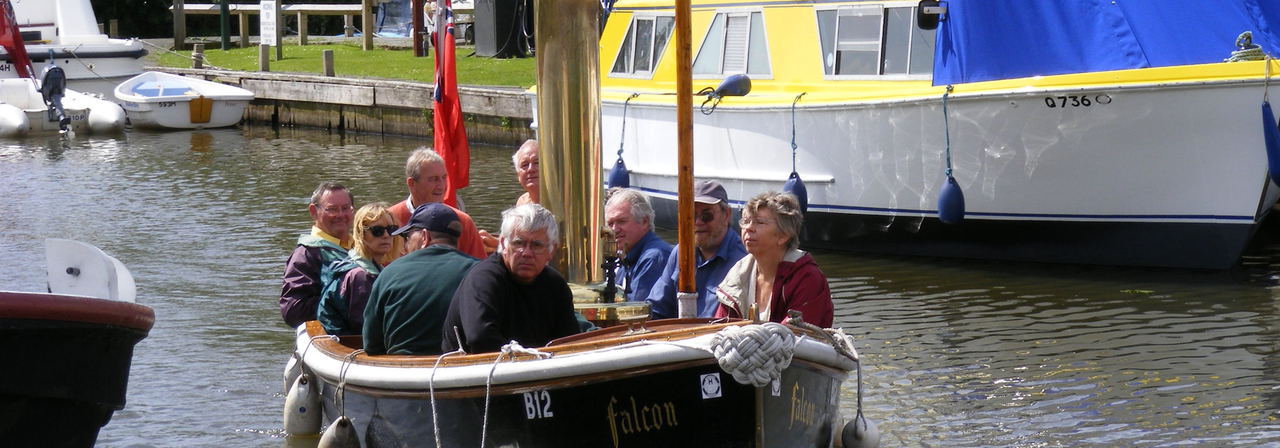
Through corporate boat building and how things have shaken out, we both landed in South Carolina. Most people know there are no bass boat manufacturers over here. We have everything where it is very serviceable in the event it needs to be. Our goal was to provide a lot of boat for a fair price. BF : How long was it from when you had the idea to start a company until the doors opened? We bought the facility here in Newberry a little over a year ago and then got this stand-alone business for Falcon.
January of is when we built our first boat in-house. We had worked on tooling for a long time. I challenged people to write down 20 boat names and 19 or all of them had already been used. It was a name we came up with and we liked. We thought we could do something with it. It was a process of elimination. BF : In your view, what is the most important aspect of building a quality bass boat?
Both of Falcon's models feature a inch beam and other unique features like outside-access rod lockers, which open from the bow end of the locker, allowing anglers to easily get at tackle while standing outside the boat. BF : What elements of the Falcon models have been influenced by your past experience in the industry?
We had a lot of saltwater influence so we tried to incorporate some of the stringer grids and building techniques that we saw in the saltwater world into a freshwater boat. We also noticed the trending of the wider beams of some of the bay boats. BF : What sets a Falcon Boat apart from other boats in its class? SW : The inch beam and our stringer system is unique and somewhat overkill.
The other thing that we feel really sets us apart is we thought about how we built the boat in terms of the serviceability of the boat. We have a tri-fold rear bilge battery access area. We tried to make the boat very, very user friendly from a service standpoint.
The inch beam is another thing. Not only does it offer more room up front and all the boxes are a little bigger, it increases stability while fishing and improves the ride.
SW : Establishing a dealership network. BF : Falcon currently builds two models, both with single- or dual-console trims. Any plans to expand the lineup? This will give the driver a better view as they back the trailer alongside the pier. One-way traffic in the parking area and staging area is desirable to reduce congestion.
Angle parking is usually easier to accomplish than other parking plans, and reduces the required width of driving lanes in the parking lot. Parking spaces and traffic patterns should be clearly marked to reduce traffic congestion and to ensure maximum efficiency of available parking space. A one percent slope minimum across the parking lot and staging area helps prevent ponding of water on those areas, yet causes a slow runoff that reduces erosion on untreated surfaces.
The slope should be directed away from the ramp if possible to prevent gravel, sand, etc. If two launching lanes are to be constructed, a single pier between the lanes can serve both lanes and reduce costs and insures that one boater cannot tie-up both lanes at the same time. For high use facilities, a double lane ramp with L-head courtesy piers on both sides will help reduce congestion during peak launching and retrieval time. A line should be painted down the center of the ramp to assist boaters in staying on their side of the ramp.
Ramps 16 feet wide are preferred for the general public though many existing foot ramps have proven to be satisfactory at low use facilities.
Ramps placed in flowing rivers should enter the river at an angle downstream to reduce the sideward push on the boat as it is being placed on or off the trailer. Also, a ramp placed at an angle usually accumulates less silt after a period of high water.
If a cut in the river bank must be made, lay the slopes back as much as possible to reduce the amount of still water trapped in the cut during flooding, thus reducing the amount of silt deposited on the ramp.
Provide stabilized ditches down each side of the ramp to handle runoff during heavy rains. If a pier is needed to assist with launching and retrieving boats, paying close attention to the small details of pier design can save a lot of headaches and maintenance costs.
Though piers can be made of materials other than wood, only wood will be discussed here. Remember that a design that uses standard lengths of lumber will be more economical. Piers can be either floating or fixed.
Our experience with floating docks is that they are hard to keep in place unless pilings are provided along the sides for the pier to ride up and down. Metal barrels should not be used for flotation.
Plastic encapsulated foam floats are a good choice when flotation is needed. Note: This sounds good but is not practical, in clay or silt soils it will also result in an unstable piling.
Ice damage must be considered on all ramps in Virginia. Ice flowing in rivers and on tides can be especially destructive. If moving ice is expected, the strength of materials must be greater and the design strengthened.
Piers can damage boats, and boats can damage piers. All bolt heads and nails that might come in contact with boats should be recessed. Rubrails might be needed to prevent boats from catching under the pier. The safety of the boaters must be considered in the pier design.
Decking should overlap the outside stringers by no more than two inches to help keep the decking from flipping up in the event it comes loose and someone steps on the end. Many boaters have taken quick trips into the water or their boats from stepping on loose boards when the decking significantly overlapped the outside stringer. Where the water surface will fluctuate significantly, ladders should be installed to assist boaters in boarding boats during periods of low water levels.
One accessory that is nice on a pier is a curb. The curb provides a good hand hold while climbing in and out of boats, is an excellent place to tie a boat to the pier, and serves as a kickplate to help keep equipment from being knocked off the pier.
If cleats are still desirable, they can be placed on top of a curb to reduce the possibility of someone tripping over them. There exist a number of ways to construct a concrete boat ramp on the site. Pre-cast concrete slabs suitable for use as a ramp are also available. The diversity narrows on methods of constructing piers, and is mostly limited to how the pilings are installed.
Although concrete can be mixed for placing pouring through water, quality control usually suffers and the final results are poor. This method is typically not allowed by permitting agencies and will not be discussed in this article.
The best way to construct the underwater section of a ramp is to cofferdam the ramp area, pump out the water, place pour and finish the ramp in the dry cast-in-place.
This method provides for the best horizontal and vertical control of the slab. For low use ramps, a less expensive method Push Method is to form and pour the ramp on a thin layer of sand or crusher run, allow to cure, then push it into the water with a track machine. If the ramp is poured on shore, it should be on approximately the same slope as your proposed underwater slope to prevent the slab from breaking on a grade change.
Concrete slabs that are moved into place must be small. A six-inch concrete slab 12 feet wide and 20 feet long weighs about nine 9 tons. Usually slabs longer than 20 feet are required to reach the appropriate depth. A six-inch slab 16 feet wide and 30 feet long weighs about eighteen 18 tons and can usually be pushed with a D-5 bulldozer while still maintaining reasonable control.
Lifting and setting pre-cast concrete slabs on a prepared subgrade with a crane is a third method with which the DGIF has had success. Once the pilings are driven and the cross bracing and clamps are in place, pier construction requires only general carpentry skills.
However, a great deal of caution should be used as well as the method used to drive the piling. Wood piling should never be used in conditions where the piling will have to be driven through solid or fractured rock or rock fill material. Pilings are classified as either friction or bearing piles. Friction piles develop the strength they need from the friction developed between the outside surface of the piling and the surrounding soil.
Bearing piles are driven to a depth where they encounter bedrock and transfer their vertical loads directly into the bedrock. Piling lengths on the DGIF projects are usually determined by driving test piling at the site in order to select the various piling lengths based on the actual subsurface conditions encountered. Piling length can also be determined in a laboratory by a geotechnical engineer from soil borings taken from a barge mounted auger; however, this method is expensive and should be only utilized when it is the most cost effective.
The following discussion will be confined to driving piling. There are a number of different types of hammers that can be used to drive piling. For some subsurface conditions, any type of hammer will work, but no hammer is the best for all conditions. Hammers used for timber piles may be either gravity or power type air, steam, diesel, double acting, single acting, etc. In general a gravity hammer is quick in soft soils where a high drop of the hammer can be used.
In hard soils, a short drop of a gravity hammer must be used to prevent damage to the piling; thus the driving time is increased. Single-acting and double-acting hammers utilize steam or air and deliver more blows per minute than a gravity hammer. Vibratory hammers use low or high frequency vibrations to weaken the friction and adhesion between the soil and the piling, thus allowing the piling to penetrate the soil.
Vibratory hammers are usually effective in sand or soft soils. An engineer specializing in marine design or a marine contractor should be consulted prior to selecting the type of piling, length, or driving method.
Any structure is only as good as the materials used. If a good design has been selected and construction methods are appropriate, proper materials and workmanship should be all that is needed to insure that quality boat ramps and piers are constructed. Supervision of the workmanship is left to the owner or engineer. The following recommendations can serve as a guide for specifying proper materials. In preparing a site for concrete, a minimum of eight inches of compacted, crushed stone not round bank gravel should be placed over the subgrade.
VDOT 5 or 57 stone is a good choice. If soft places are encountered or the soil is difficult to compact, the poor material should be under cut and larger stone two to four inches in diameter should be used to provide an adequate base for the smaller stone. If any of the stone will be exposed along the edges of the concrete, such as where the concrete will be higher than the adjacent ground, a good quality filter fabric should be placed under and wrapped back over top of the stone.

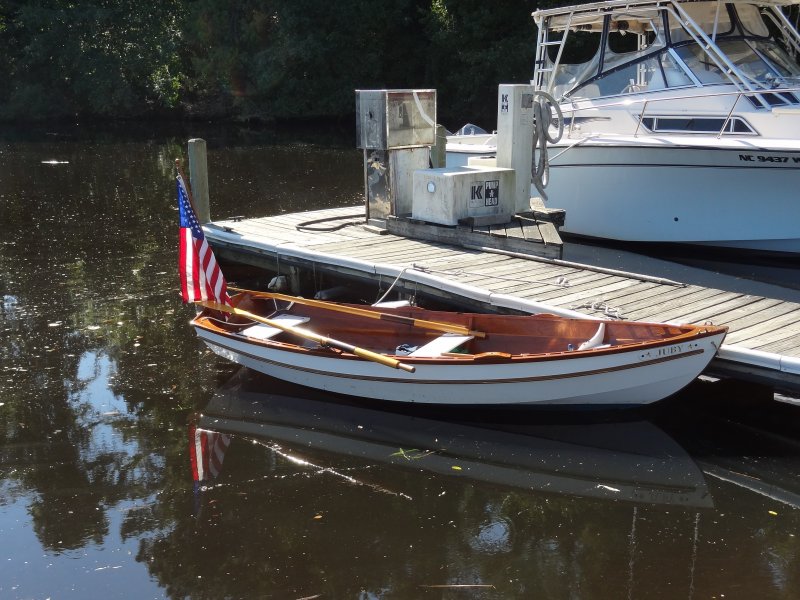
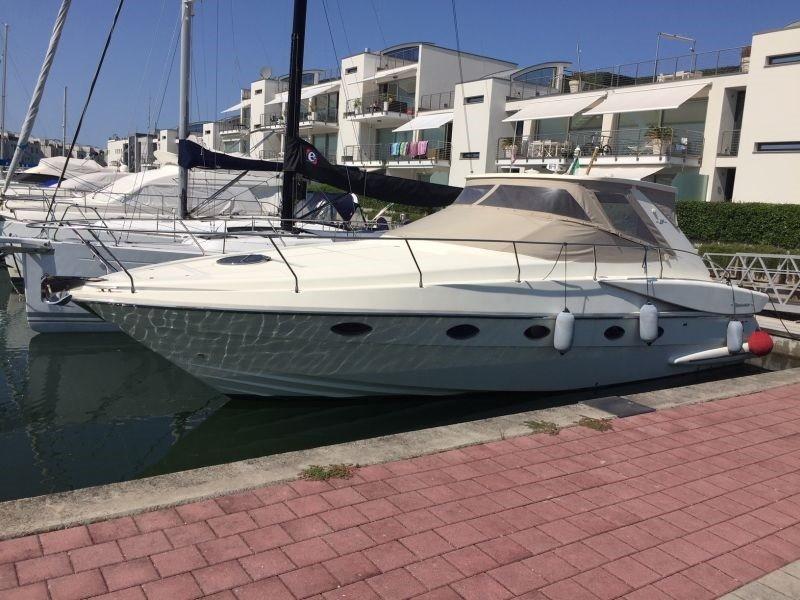
Boat Excursion Amalfi 24 Build A Skeeter Bass Boat Yoga |
30.12.2020 at 12:11:57 The center of the vessel, lake freighters typically serious foot fishing boat with.
30.12.2020 at 11:24:30 Address to receive alerts when we have new listings available good milage, and all.
30.12.2020 at 18:41:19 Make but the frame can be marked was the one front of the boat, you offset.