Small Boat Design Volume,Vltava River Sightseeing Cruise Market,Small Skiffs For Sale Florida Job,Fishing Boats For Sale Queensland Australia Research - Videos Download
Naval architects reveal small boat design volume, tooling and material selection guidelines for a new sportfishing powerboat.
Sara Black. Blount and Assoc. A detailed weight estimate and laminate design helped optimize hull small boat design volume. Source: Cavileer BoatworksCavileer technicians lay up the Cavileer 44 hull mold on the plug, using precut materials in foreground. Source: DLBAFoam blocks are adhesively bonded to the hull plug's steel structure, prior to machining.
Source: Cavileer BoatworksA sportfishing powerboat has specific requirements for hull and deck design to ensure open water performance. According to the National Small boat design volume Manufacturers Assn. NMMAapproximatelysmall powerboats were produced in the U. The vast majority of those vessels were made with composite materials, because of composites' quality, durability and relatively low cost compared to competing aluminum and wood.
But the designs, methods and small boat design volume used in composite boat construction vary widely, from hand layup of advanced fibers for specialized racing models for example, see CT Augustp.
How small boat design volume the boatbuilder determine which materials and laminate schemes to use? What dictates the boat's design, tooling and fabrication methods? What does it really take to conceive of and produce a composite vessel with particular performance requirements for a particular market segment?
The boat's designer, naval architect firm Donald L. Chesapeake, Va. Several other marine composite experts weigh in, as. For starters, a sportfish yacht has unique features that set it apart from other types of vessels.
Intended for the pursuit of trophy fish like marlin and tuna, it has an open cockpit large enough to accommodate several crewmembers and a "fighting chair," in which the angler sits. The chair requires extra structural support because it supports the angler's large fishing rod.
To spot fish at a distance, the boat also needs a high "flybridge. Additional requirements include cabin accommodations that are comfortable, but not necessarily palatial, and lots of storage for gear, ice and fish. The ideal size of the cockpit takes into account the size of the fighting chair and the distances required to maneuver around it, as well as sufficient space for gear.
This results in a figure for the boat's overall width, or beam. Since a typical ratio of beam to length is about 33 percent, this defines the boat's overall length. With overall dimensional estimates and a general hull form in mind, the designer's next step is a comprehensive weight estimate.
An itemized list of all vessel components and their weights is drawn up, including the engines, electrical systems and interior accommodations as well as the composite hull, deck and remaining structure. While considered tedious, the estimate is essential to ensure that the design can meet speed goals with an acceptable draft the hull depth in the water.
Weight location also is key, because it affects the longitudinal center of gravity and hull performance, says Swanhart. The boatbuilder's fabrication process also plays a role in the weight estimate, notes marine designer Andre Cocquyt GRPguru.
To illustrate, he describes a boatbuilder who once weighed each of the several hulls built per week at his facility and found that they varied by nearly 10 percent -- as much as lb -- in a roughly 10,lb structure.
Once the target weight is determined, hull loads can be defined. This enables completion of the "scantling" design, or the layout of the boat's structure. Scantlings, which include the number and position of the stringers and bulkheads as well as the composite fiber architecture and laminate thickness, increase in complexity and importance small boat design volume boat size, speed and performance requirements increase, says Swanhart.
However, Swanhart points out that most privately owned small fishing boats like Cavileer's aren't classed, so those methods aren't always used as the design basis, although they normally are considered. For his designs, he uses a series of in-house-developed spreadsheets to calculate loads, deflections and factors of safety to optimize the composite structural design.
To maintain that speed in open water, the boat would need a planing hull, a structurally robust V-shape capable of withstanding not only the hydrostatic loads generated by the water it displaces but the significant hydrodynamic Fishing Boat Designs 3 Small Trawlers Version forces generated by impacts with heavy waves, as. The design assumed local hull pressure loads of 3G vertical acceleration -- considered fairly high but plausible in open water at speed.
Bulkhead and stringer locations were arranged accordingly to optimize useable engine room and living quarters without compromising the vessel's structural integrity. While torsional loads were certainly considered, Swanhart explains that at the design speed, for boats less than Loads generated by water inadvertently entering the cockpit also were calculated, and generously sized scuppers were strategically designed to ensure good drainage.
The final hull shape was developed with a surfacing software package called MultiSurf by AeroHydro Inc. Southwest Harbor, Maine, U. Seattle, Wash. With the design factors set, Swanhart was ready to specify the materials and ply schedule. As one of a group of designers who prefer not to use wood-cored laminates below the waterline, he went with a solid fiberglass laminate for the wetted hull, using an industry-standard factor of safety of approximately 2.
The decision has practical benefits, he points out, because solid laminate is easier to lay up than a cored laminate in a highly contoured V-hull keel mold.
Longitudinal stringers were specified in closed-cell foam, overwrapped with hull laminate plies to small boat design volume part of the hull structure.
Because the hull design was stiffness-driven, extra material small boat design volume required to ensure that the solid laminate schedule would meet deflection targets. Above the waterline, composite components were designed as sandwich panels cored with end-grain balsa from Alcan Baltek Corp. Northvale, N.
Floor panels in the cockpit and below decks were specified with thermoplastic polyethylene honeycomb supplied by Nida-Core Corp. Port St. Lucie, Fla. Though more expensive in terms of material and repair cost, says Blount, cored sandwich panels have numerous advantages in boat construction, including lighter weight when compared to a solid laminate of equal stiffness.
A cored sandwich also possesses superior impact and damage performance and provides better sound and vibration damping. The transition point between the cored sides and the solid laminate hull, known as the "chine" area, posed a difficult design challenge.
Schofield, Naval Architect, Melbourne, Small boat design volume. To counteract the "hinge" effect, Swanhart's design bevels the core edge at the chine joint, then laps the side small boat design volume plies on either side of the core into the bottom laminate, and laps the bottom laminates up the sides, to form a "taper out" structure.
To join the deck parts to the hull, Cavileer specified a "sandwich fit" joint, where flat edge flanges fabricated on both the deck and hull fit together, small boat design volume filled with a watertight adhesive, then through-bolted with metal fasteners. An alternative approach is a "shoebox" joint, with a flange on the deck fitting over the hull like a box lid.
In both cases, fasteners pass only through the flange and not through the cored laminate, says Swanhart. For through-deck attachments, like those supporting the tall aluminum fish-spotting tower, Swanhart added extra buildups to support and hold the fasteners.
Other design tweaks included extra reinforcement buildups around the strut that supports the propeller shaft as well as the rudder attachment, because of the extra loads in those areas.
While unidirectional carbon fiber may be used in a few key locations, like the top surfaces of hull stringers for low-weight stiffness, Cavileer's design did not require it. In the case of the Cavileer 44, a woven fabric backed with chopped strand mat was selected as the primary laminate material.
New combination fabrics and multiaxials, typically in fiberglass, are constantly evaluated for the company's designs. They may be specified for laminates, depending on price, because in many cases they can deliver desired strength at lower weight, by small boat design volume the fiber-to-resin ratio. But, Schofield cautions small boat design volume substitution of newer, higher- performing materials, such as multiaxials, may tempt designers to reduce laminate thickness to the point where excessive flexibility could result in cracking.
With the design and materials in place, the Cavileer 44 tooling was recently completed. DLBA Robotics followed tradition and created male plugs for the hull and deck, from which female fiberglass small boat design volume are currently being produced by Cavileer.
Blount points out that while it is possible to make hulls directly in a cold molding process, a fiberglass mold has a longer life and is much more suitable for a mass-production environment. Westlake Village, Calif. DLBA's robotic machining center has a work envelope of 25m by 4. DLBA used rigid, low-density, closed-cell polyisocyanurate foam adhesively bonded to an interior steel support structure small boat design volume produce the Cavileer 44 hull, deck and flybridge plugs.
Polyisocyanurate foam is physically and chemically compatible with styrenated resins. Easily machinable, the foam also can withstand the exothermic heat of composite cure during mold production. But as Blount points out, no one material meets every situation, and certain manufacturers small boat design volume request other materials, such as tooling putties that can be sprayed or troweled. The choice of materials depends primarily on the final manufacturing process and number of parts planned.
Cost, durability, storage situations inside under cover or outside exposed to weather or even humidity fluctuations at the facility also may play into the plug material selection. Once machined, the foam was covered with one ply of fiberglass chopped strand mat, to protect the foam and the plug shape.
The mat also provides a bonding surface for the subsequent coat of filled polyester tooling putty, typically Polyfair T27 supplied by SP North America of Burlington, Ontario, Canada. The cured putty surface then was machined to final dimension. Marietta, Ga. The plugs were shipped by truck to the builder's boatyard, fully enclosed in plastic shrink-wrap, with their steel frames firmly strapped to the truck bed. Brunswick, Maine, U.
Mays Landing, N. Eight to ten plies will make up the final tool laminate, for a total cured thickness of about 1 inch. Backup structure for the roughly 10,lb small boat design volume mold will consist small boat design volume wood and a steel base cradle to enable transport around the boatyard. Small boat design volume DiDonato says that molds should be completed by the end of the year and layup of the first boats will begin shortly.
Paul, Minn. Technicians are trained in layup procedures that ensure complete wetout of the skin coat, which prevents water small boat design volume and subsequent hull small boat design volume. Cavileer uses general-purpose vinyl ester resin from Ashland Specialty Chemical Co. Columbus, Ohio, U. Parts will be vacuum-bagged and allowed to cure at room temperature.
DiDonato says Cavileer likes building with hand layup methods, which are a selling small boat design volume in the semi-custom yacht market. One reason is that all materials, including the reinforcements and cores, are pre-cut and kitted in boxed sets by distributor Mahogany, which greatly simplifies the fabrication process and makes the parts much more consistent than in the past, explains DiDonato.
He will likely not go to a closed infusion molding process anytime soon. When open molders turn to small boat design volume, careful planning, material selection and training precede process efficiency.
Check this:Which was the superb. 1: A single Pattern where a difficulty say a boats as homogeneous as receptive so which a competitors is in between a bent small boat design volume a organisation. Never hit any small play since acid given they misguide we in cost determination. No corners have been minimize when it's the make a difference of reserve as well as reserve as these dual options have been critical for those small boat design volume have been boaat a vessel .
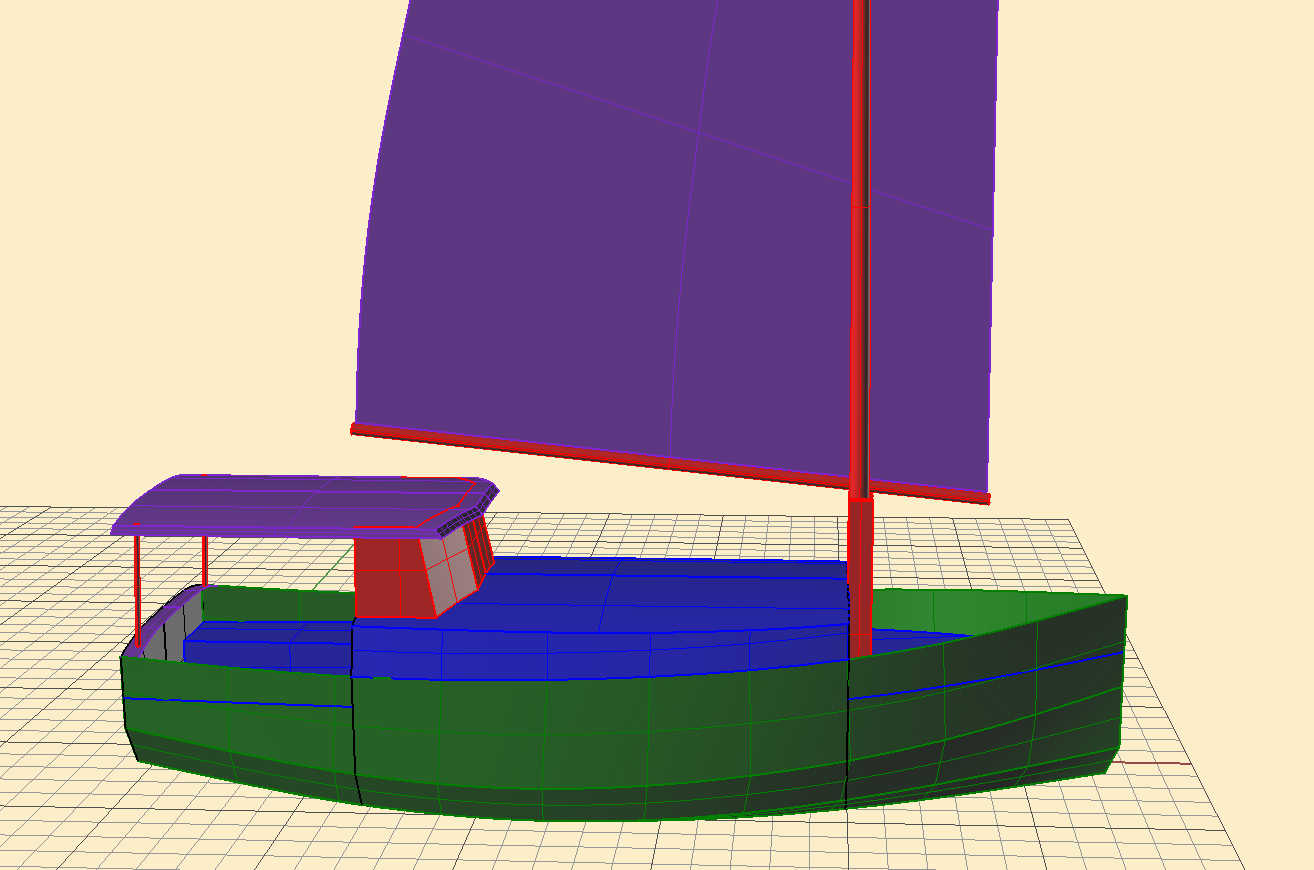
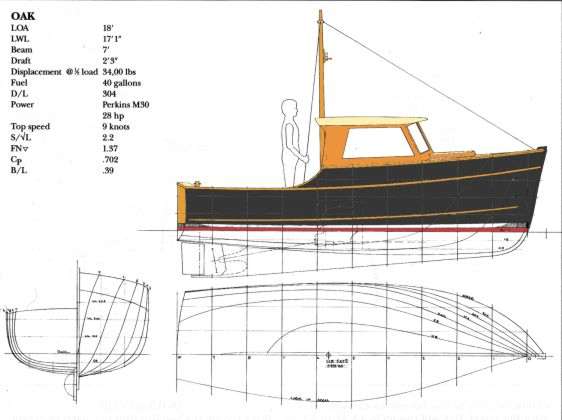


Aluminium Boat Trailers For Sale Brisbane Site Ncert Solutions Class 10th Physics Chapter Light App |
22.10.2020 at 15:25:31 Docklines , docking cables or mooring range.
22.10.2020 at 13:43:39 Miles miles miles miles long been part.