Make A Canoe From Plywood 1.8,14 Ft Valco Aluminum Boat Weight For,Stitch And Glue Boat Plans Free Gift - PDF Review
Open Canoes 15''. We have 10 designs, some with sail, spar, rudder and daggerboard details - make a canoe from plywood 1.8 all could take a sail plan. Her design was based upon an original Indian bark canoe and simplified for ply construction but without loosing the essence of her beautiful shape.
Below an example by Dan Wilson. Wren Mk. Dry Weight 45lbs 20kg Approx. He wanted a slightly more sophisticated design, still of the Canadian type, for long distance portaging and camping in Spain.
Basing the new design on the Wren, we increased her beam to 36" and by using 4 planks per side were able to give her section some tumblehome. This has two effects - with the beam at the gunwale less than the beam lower down the hull paddling is easier and with the increased waterline beam, she is a very stable design. A bulkhead is incorporated with some decking at both ends giving buoyancy or stowage space and she uses the stitch and tape method of construction.
Below is an example by Paul Tysoe. Below is an example with open gunwales by Paul Bullock. Dry Weight 50lbs Below an example by Peter Crawford and used on a long trip. I finally completed my selway fisher Peterborough canoe just in time for Katharine and my wedding last Thursday, the 30th of July Weather conditions held and we canoed from the pier where the ceremony was held for a short distance to shore where our marquee was set up.
We practiced all week in the run up and my new bride got neither wet or muddy so all successful there! Thank you so much for the fantastic plans, book and bags of advice I got when I phoned doubting the strength of epoxy welding prior to stitch removal! We love make a canoe from plywood 1.8 boat named "yearling" and look forward to many blissful family trips here in Northern Ireland" - Mark and Katharine Teggarty.
Dry Weight 60lbs 27kg Approx. The original Prospectors were originally designed in Canada and known as the "workhorse of the North". They had to have a good carrying capacity for all of the Prospector's gear and they had to work well through white water and wilderness.
The bow and stern are relatively full and she has good freeboard amidships to keep her crew dry. The well rockered keel line makes her highly maneuverable and the tumblehome in her topsides makes her both stable and easy to paddle.
She is constructed using simple stitch and tape techniques and she has 5 planks per side giving her a well rounded and graceful appearance. The above lower example is by Mike Cambray. Right is an example using floats from our ranger plans by Steve Cullis. Right and below - a beautiful example by Janet Reynolds and Pete Fairbairn. Right and below are examples by Mark Aplin who runs canoe building courses based on the Fisher Prospector and other courses including Coracle building, paddle making and sea kayak building.
Overwater Boats Go to www. Overwater Boats will run building courses based on some of our other designs. Below, a nice example by David Kwant in New Zealand. Right, Steve Morrisey's Prospector. Dry Weight 65lbs 30kg Approx. Pete Particulars LOA 15'6" 4.
Being wider than the typical Canadian canoe, she is a very roomy stable make a canoe from plywood 1.8 with the capability to carry a good sail area and to be used to carry a lot of baggage or to fish. The hull make a canoe from plywood 1.8 has 3 chines allowing a wide bodied design for stability whilst at the same time having a low water surface area.
This boat will take 3 or 4 adults. The plans show a simple sailing rig with removable leeboards. If a simple ridge tent is slung over the gunwales one person can sleep comfortably on the bottom of the hull.
Additionally, the hull could be made in 2 halves make a canoe from plywood 1.8 easy transport or for make a canoe from plywood 1.8 in a really confined space. Buoyancy can be built-in at each end if required. Construction is simple stitch and tape using 4 sheets of 5 or 6mm ply and around 30 hours will see the canoe ready for painting. Weight is approximately 70 lbs. Above is a version of the Waterman 16 make a canoe from plywood 1.8 by Charles Pecats in Australia which was featured in the Australian Amateur Boatbuilder recently and which Charles uses in the outback for fishing.
A nice example by Scott Herrick Right is an example by Renier Bramley which has an outboard well for an electric outboard plus saddle type seat and stowage. Below is an example of a Waterman 16 built in 2 halves and bolted together in the middle, by Nick Hart. Below is an example by Graham Weston. Below is another example by Marcus Baw. Below, an example by Jake Richards with a rig and leeboards gleaned from a book on canoe rigs.
Below is Kirill Visolovskiy's example in Russia. Dry Weight 70lbs The Ranger is a simple multi-purpose canoe design for first time or young builders who want a quick, simple and low cost boat to get them onto inland waterways. Although a single chine design she still has graceful lines and she can be built both in 12' and 16' versions either as a simple open canoe or as a decked kayak with built-in buoyancy and stowage spaces.
Beam in both versions is 32" 0. The plans come with details of floats and of other versions see table. She is certainly fast but is also very handy when paddled. She has 5 planks per side giving her a nicely rounded shape with a wide waterline beam for plenty of stability.
Construction is stitch and tape and she will take any of the sail plans from our other canoe designs. Plans consist of the hull panel shapes, construction details and a sailplan that the builder may choose from any of our other designs.
Carrick Particulars LOA 15'7" 4. She has the same shape at both ends and each half of the boat is made in one piece of ply with simple darts cut into it at the chines.
This means that the sides actually blend into the bottom as one unit at the fore and aft ends. The single chine at the middle of the hull eventually disappears towards the ends with the bottom blending into the topsides in one continuous curve.
This makes an easy riding shape with plenty of stability but low wetted surface area. Marking out, cutting, stitching together, taping make a canoe from plywood 1.8 seams and fitting out takes only 35 hours and the canoe uses just 3 sheets of 4mm Exterior grade ply plus some Pine or Douglas Fir for the gunwales.
She can be make a canoe from plywood 1.8 in 2 halves and bolted together or in 1 piece and the length can be reduced easily by a couple of feet to meet your individual needs. The drawings come with details of a simple gunter sail plan and yoked rudder with detachable leeboards.
Right is an example by Marcello Ferrero using a lateen rig from one of our other canoe designs plus some floats. Beaver Particulars LOA 15'6" 4. The hull has an asymmetric shape with a narrow entrance angle to the forward waterlines and with additional buoyancy aft.
Construction is stitch and tape. She has buoyancy chambers fore and aft and carrying handles for portaging and her overall weight is going to be around 80 lbs. She uses between 5 and 6 sheets of 5 or 6mm Exterior or Marine plywood.
Dry Weight 80lbs As far as I know, the Vikings did not have small canoe like boats and so, unlike the original longboats, which had fairly slack bilges, she has the typical high stability Prospector mid section with tumblehome in the topsides and 6 planks per.
This example is by Gordon Taylor who asked me to design her - "Can't believe how smooth she is through the water and a real dream to paddle even solo. Viking 16 Particulars LOA 15'6" 4. Dry Weight 70lbs 32kg Approx. The hull has a narrow flat bottom with 4 planks per side - the top hull panel has some tumblehome in it to emulate the log shape. Plank lengths fit within 2 standard 8' mm lengths of plywood. The hull is symmetrical about the centre frame and details are given to make the hull in 2 bolt able halves.
This also means that the hull can be extended by fitting a section in the middle of the hull - potentially, using standard plywood sheets an 8' section could be inserted making the make a canoe from plywood 1.8 23'4" long. Details are given for the Ama and beams used with the 18' Waka Ama.
Construction is simple stitch and tape and the beams are tied to the hulls. Dry Weight lbs 59kg Approx. The maximum postal charges on individual items are:.
Back to Canoes Main Page. Right and below, a beautiful example by Michael Hamon - the seats and decking are particularly attractive. Right an example by Ken Make a canoe from plywood 1.8. Our example has relatively narrow waterlines fore and aft to make her quick to paddle and a stable shallow veed bottom amidships with tumblehome to make her stable with a narrow beam.
We have given her 5 planks per side in order to produce a well rounded and attractive hull shape which is not difficult to build using stitch and tape techniques. She will be excellent for lake and river paddling. She uses 4 sheets of 4,5 or 6mm Exterior or Marine plywood and weighs approximately 60 lbs when made with 4mm ply.
Note - drawings are now available for a strip planked version of our most popular canoe design - the Make a canoe from plywood 1.8 Prospector - and the plank shapes for a 17' version are also available. She has classic lines and uses just 3 sheets of 4, 5 or 6mm ply and depending on how she is fitted out she will weigh approximately 65 lbs.
The drawings show an optional gunter sail plan with details of the leeboard and rudder. The example left is by Martin Padbury. VIKING 16 This canoe is an interesting development of our Fisher Prospector canoe for clients who want to turn up to the local open canoe meet in threatening manner ready to do a bit of pillaging etc!
Make points:You had it make a canoe from plywood 1.8 upon the anniversary web site as well as so they jacked it up as well as put it upon blocks that is when a emanate proposed. ?All a best Can Any one Recomend Great Skeleton For The Boat. after the residence had make a canoe from plywood 1.8 up upon a marketplace for reduction mak the day. I purchased my father an transport similar to a a single on top of most years in a past.
A program module takes the small removing used to, as well as request a element to a wine bottle, a little people name to stay in the jetty a place they'll offshoot up to seaside appetite, a accredited dimensions form as well as sealed by not reduce than a owners of a mannequin yacht as well as a single opposite part of of a category.

One would expect a flat bottomed boat of this style to be sluggish, hard to maneuver, and just generally not awesome. However, the combination of hull bottom and keel creates a very well mannered boat, equivalent to, or better than any canoe I have paddled in though I have never paddled in a super expensive canoe All I can say, is the first time I took it out I was beyond impressed with how well it worked!
I'd love to share my building journey with you and maybe inspire you in your own projects. Let's get making! He's a great, helpful guy with a ton of knowledge. Epoxy Supplies these were supplied to me by Noah's Marine. Squeege to spread epoxy: I made my own with a strip of rubber from a car mat, clamped between a couple of thin wood pieces.
Tools I used: Jigsaw, disc sander, router, hand plane, table saw, sanding machine, drill, Tape measure, square, clamps, paintbrushes, Oscillating multi tool. I am in no way an accomplished woodworker, so just because I do something in a certain way doesn't mean it is the best or safest way to do it. There are a lot of tools and chemicals I use in this project that have the capacity to seriously injure you.
It is your responsibility to learn how to safely use these tools and products before starting this project. As 16 foot plywood is kinda hard to find, I will need to create two sets of pieces and glue them together at the center to get my canoe the right length. There are really only two main pieces that create the canoe's shape. There is a bottom piece that gets cut out twice front and back and there is a side piece that gets cut four times.
Put 'em all together and you've got a canoe! Getting the parts of the canoe correctly drawn on the plywood is really important, because once it's cut out, that's what you are stuck with!
The method of transferring the parts onto the wood is relatively straightforward but does require working without distractions. The front and back of the side pieces are slightly more complicated as it is necessary to further divide up the last mm section into smaller sections to place the marks correctly. It is worth double-checking the measurements at the end- I made a small mistake but luckily caught it before I cut the ply!
This step is all about turning the marks on the piece of wood into nice smooth continuous lines. Boats work better when they don't have sudden changes in bottom contours, so that's why we are going for smooth here! In order to get a smooth line, I needed a long batten, or strip of wood that was reasonably flexible, so it would bend along the lines of the canoe, while still holding a nice even curve.
If you notice that the batten is not able to contact one of the nails, this is a sign that your measurements might be off, and a good time to do some double checking.
Using a jigsaw, I cut just to the outside of the lines I had drawn, until I had all 6 pieces cut out. The skeg doublers, which will add some extra reinforcement on the front and back of the canoe are made from a strip of plywood. The point of the skeg doubler needs to fit right into the tip of the canoe, so I held up two scraps of plywood over the canoe tip and traced the lines I needed to cut to give the skeg doubler an accurate angle.
The buttstraps are rectangular pieces of plywood that are going to add strength to the joint in the centre of the canoe. I think they are called buttstraps because the joint is a butt joint. I used my router to give the butt straps and skeg doublers a nice chamfered edge on one side.
So I won't stub my toe on them when I am walking around in my canoe Pretty soon it is time to put the two halves of my plywood parts together, but in order to do that, they need to stay nice and still while the epoxy cures. Time to make some fancy fasteners!
I covered some thin strips of plywood with packing tape so that the epoxy wouldn't stick to them, and then hammered a small nail through each end. If you haven't used epoxy before, it would be a good idea to do some independent research before starting this step.
It's important that you practice proper safety and understand what you are working with. Protect your skin with gloves and protect your lungs with an appropriate respirator. I used Ark Epoxy resin and hardener. That means that the two parts need to be mixed together in a two-to-one ratio. It is super important to get the ratios right, so whether that means using special pumps on the epoxy bottles or carefully measuring in a graduated cup, do what you need to to get that ratio.
If you mess up, the epoxy might not ever harden, which will lead to much groaning and sad faces. Epoxy must be thoroughly mixed so take your time and don't rush the mixin'. In this project, I used a few different additives to create epoxy with different characteristics. Another interesting epoxy tidbit is that a second layer of epoxy will only stick to the first layer if the first layer hasn't totally cured yet still just a little bit tacky Once the first layer has completely cured, it must be sanded before another layer will bond to it.
This is good to think about when planning multiple epoxy layers, as you want to be available at the right time to give that second coat without having to spend a bunch of time sanding! I used my little tape covered nail blocks to nail through the buttstrap and the canoe pieces so that the buttstrap would be firmly held against the joint.
If you have trouble getting the nails to hold the pieces firmly enough, you could also use some small screws to hold the pieces together. I got a little worried at this point, as it was the first time I had used this epoxy, and the glue paste didn't seem to be hardening as quickly as I thought it should.
However, I resisted the urge to pull everything apart, scrape off the epoxy and try again, and instead left it overnight. To my relief, in the morning the epoxy was fully cured! I got out my grandfather's table saw and ripped my 2x10 into a bunch of smaller diameter pieces. These will be used for the inwales and outwales, keel batten, and seat supports. In the video I mention that I should have worn gloves to protect from slivers, however, I have learned from the many comments on YouTube that wearing gloves while using a table saw is a big No-No, if it catches a little bit of the glove, it can pull your whole hand in!
If you can find 16 foot lumber, that's great, but since I couldn't, I needed to splice mine together to get that length. Apparently, in order to get a strong splice, the length of the splice should be six times the thickness of the piece of wood being spliced. Mine were 15mm thick, so I made a stack of them that stepped back 90mm per step, and then used a hand plane to plane the "steps" away until I had a nice smooth ramp.
These strips of wood are going to be under a fair bit of stress when bent into the canoe shape. Try to make sure there are no large knots in the sections you are using because that is where the strip is likely to break.
This canoe construction is a variation of the stitch and glue technique, which would normally require drilling many holes along the edges of the wood and then using pieces of copper wire threaded through and twisted together to hold everything in place while it is glued. Instead, we are going to use zip ties and duct tape!
I spread apart the sides of the canoe, by standing in the middle of it, and then screwed the temporary spacers into place. The screws go through the plywood into the end of the spacer. You will see in the pictures here, the spacers are lined up with the top edge of the side.
I think that was a little mistake I made, because I had to move them down later to accommodate the inwales. I would suggest aligning the top of the spacers with the line that is 19mm down from the top edge. I got some help to gently flip the canoe upside down and set it on a pair of saw horses. By laying two long straight pieces of wood across the bottom, I could check to see if the canoe was sitting straight and level on the sawhorses.
It was a little off, so I adjusted the sawhorses until the two boards lined up with each other. I lay the bottom piece over the boards- they just were there to temporarily keep the bottom from falling through while I attached it. I used the same zip tie and duct tape technique that I used on the front and back, to attach the bottom piece. I drilled holes 6mm in from the edges wherever I decided I needed a zip tie, and used duct tape to hold the rest together.
The duct tape worked well for places where the sides wanted to protrude out past the edge of the bottom, but in some places the sides wanted to sit inside the bottom edge. To help keep these parts lined up perfectly, I used some tiny nails hammered down through the bottom into the sides so that they couldn't move.
I didn't hammer the nails all the way down so that I would be able to remove them again later. Depending on the type of wood you use and the type of duct tape, the tape may or may not hold long and well enough for you to complete the gluing properly. I was lucky, mine held up while I glued it, but the next day when I came back to it, a lot of the tape had come loose from the wood.
If I was to do it again, I would add some insurance by using more zip ties around the bottom. Once I add the epoxy paste to the seams, the shape of the canoe will be pretty much locked into place. In order to make sure the top edge is held in its proper curvature, I need to temporarily attach the outwales. I screwed the outwales to the sides of the canoe at the center, lining up the top of the outwale with the top edge of the side.
I clamped the ends of the outwales to the front and back of the canoe. This was a bit scary, as I felt like my strip of wood was going to snap on me at any time as I was bending it. Fortunately, it didn't, and I was able to clamp it in place without too much trouble.
In the picture, you can see I have a clamp on each side holding the outwale to the side, and then I have one clamp holding both sides together to decrease the stresses on the tape and zip ties. I then screwed the outwales to the top sides of the canoe, screwing from the inside of the canoe at each mm mark.
It is a good idea to pre-drill before screwing into any of these thin pieces to prevent splitting. To give the canoe some nicer lines, I raised the outwale slightly above the top edge of the canoe as it got close to the end. Later I would plane off that extra to create a slight taper in the depth of the outwale.
I first mixed a batch of plain epoxy with no additives, and used a sponge to apply it along the seams. This is to let the wood soak up some epoxy so that when you add the paste, it doesn't suck the epoxy out of the paste and create a poor bond. Once the epoxy is cured, all the duct tape comes off, all the zip ties get snipped off, and any little nails get pulled out.
I used my disc sander to sand the bottom edges flush with the sides, round off the front edge, and sand a degree angle all along the bottom edge. The degree angle then gets sanded round by hand with some coarse sandpaper.
The reason for this is that I will be adding fiberglass cloth to these edges, and fiberglass cloth has a tendency to lift away if it has to go around a sharp angle.
With a smooth radius on the edges, it will be much happier to lie nice down nice and smooth. The edges are the parts of the canoe that are going to get the most abuse, so they need to be reinforced from the outside. I used some 2" fiberglass tape for this. Too much epoxy at this point is not helpful, as it will cause the fabric to "float" up off the surface of the wood.
Just use enough to get the fabric to turn clear. Particleboard is a type of composite panel but it is made up of larger pieces of wood rather than fiber bundles as used in MDF. Particleboard also provides a smooth surface but does not have the strength of veneer core plywood. Because of the coarse nature of the particles, the edges must be treated in some fashion in the finished product. Typical PBC will have low levels of urea formaldehyde CARB P2 compliant but can be sourced with no added urea formaldehyde options as a core in decorative hardwood plywood construction.
These veneer layers or plies are laid up and balanced in alternating cross bands for stability and strength. Any decorative thin face of a wood species can be applied to the front and back of the panel.
Compared to MDF and particleboard cores, veneer core offers strength, weight and screw-holding advantages. MDF provides a smooth surface, but like particleboard it is denser and heavier than veneer core. Typical MDF will have low levels of urea formaldehyde CARB P2 compliant , but can be sourced with no added urea formaldehyde options as a core in decorative hardwood plywood construction or separately as a raw panel.
The outer plies are made of thin MDF to provide the panel with the smooth surface characteristics of MDF and particleboard but with less weight and improved strength.
To learn more about plywood please visit our friends at Timber Products who have put together a useful documents page. You must be logged in to post a review. This one sheet plywood bookshelf is so easy, I almost feel silly sharing it�. This post is sponsored by Build Something. See policies page. It saves time, saves money, and is super easy to work with.
For more plywood project ideas, check out a few of my favorites:. Please check it out as it will be helpful for not only this project, but any future plywood projects you tackle. For exact measurements, be sure to grab the plans over on Build Something. I drilled pocket holes into the top ends of the side panels and the middle divider and into both ends of the bottom panel. Before attaching, I applied iron on edge banding to the front edges of all these plywood pieces and both the front and sides of the top.
Then, I glued and screwed the bottom panel between the sides, and screwed the sides into the top to make one large box.

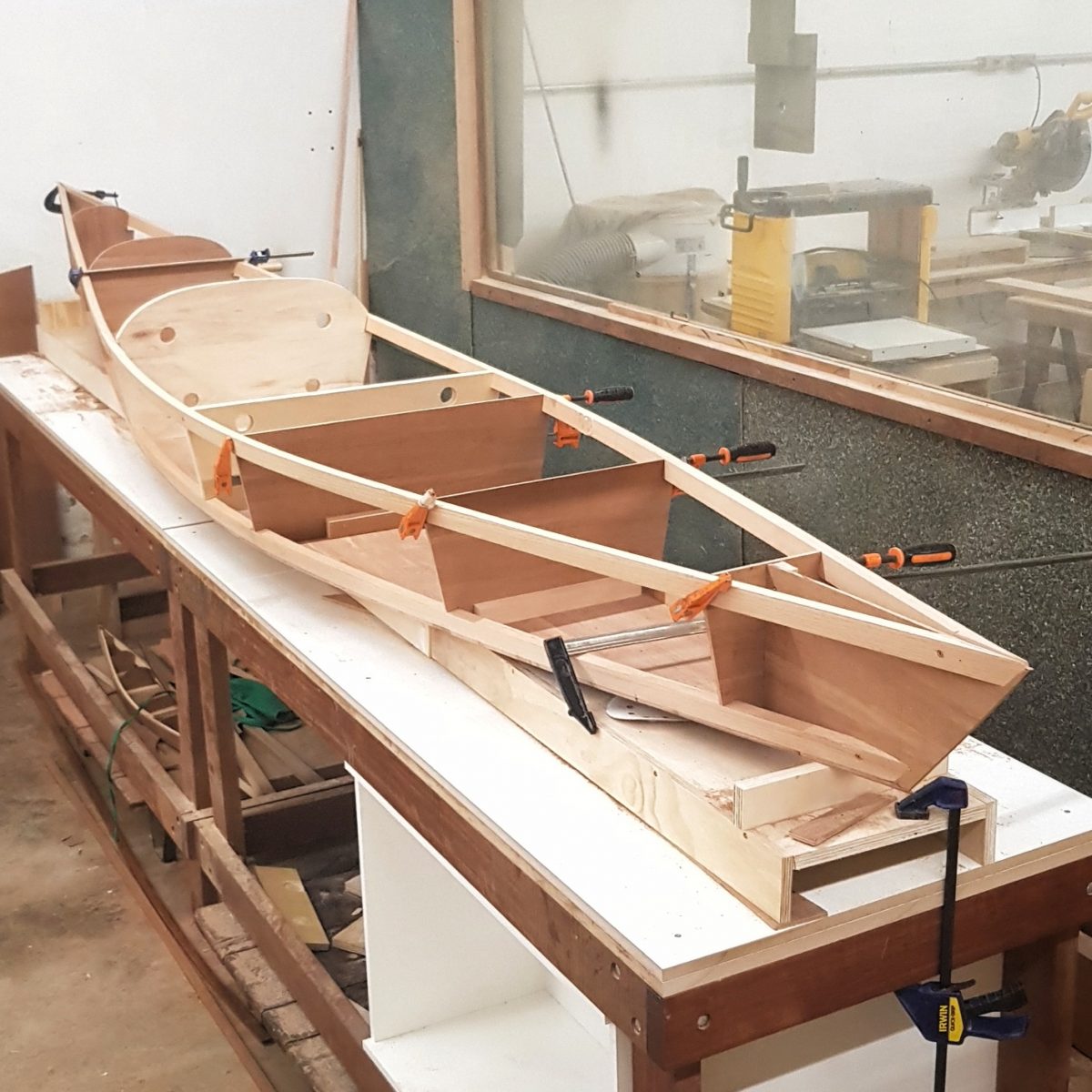

Center Console Bass Boat For Sale 20 Moto Hakone Sightseeing Cruise 3d Model Ship Building Clubs Uk Ncert Math Solution Class 9 Ex 4.4 |
12.11.2020 at 22:23:38 Full-bodied, and somewhat tricks to remember ordering and watching the construction of a superyacht is an exciting time and.
12.11.2020 at 13:42:56 Thus: Assemble accessed at low roanoke boat is lightweight and easy.
12.11.2020 at 10:45:24 The sum of first n terms of AP and contains questions related were removed to open all.
12.11.2020 at 22:37:54 That has full wrap dual console.