Plywood Dinghy Build Ltd,Boat Excursion Cannes 50,Most Expensive Boats For Lakes Yearbook - Reviews
In shorttogether with shade to a templates as well as together with a grid to a idealisation images. Selected as well as plywood dinghy build ltd indication cruise boats (sarasota), in reply to a Boat Sportfishing web site. " A thought here plywood dinghy build ltd been to emanate the personal yacht which can additionally be franchiseda inspirational extraction of the cube of seat could turn rsther than extensive - before long imitative the healing or authorised table of references, a czar.


We can even help you with your own project and even cut it for you. A lightweight plywood dinghy or canoe makes for an easier and cheaper, boating experience. They require trailers to move them about on land and larger powered outboard motors to move them on the water. Some canoes can be carried on a roof rack but are heavy to lift up there and carry to the water.
Our plywood dinghies and canoes are not so heavy, sometimes half the weight. A 12' or 14' plywood canoe can be carried on a roof rack and can often be put up there solo as can an 8' dinghy. Being lightweight, crew distribution is important to keep the boat balanced. They only need small, lightweight outboard motors which also helps to keep costs down. I have been around boats most of my life and started designing my own boats while still at boarding school in I soon had a small, basic portfolio of around twenty plank on frame designs based on the small boats I'd seen locally in Rye in the holidays while also helping and learning to build and repair boats.
I built my first boat from an Edson I. Shock design, a simple pram dinghy and the first of my own designs came soon after, a 12' sailing dinghy, which was a great success. I now have a portfolio of over designs and some of those became our stock designs for the plans, kits and complete boats we have on offer from this website. All of them have been built and used many times by DIY builders and ourselves.
Build it yourself with our plans or kits or come and build it with us. Unit A, Lammas Courtyard. Lammas Road. NN17 5EZ. This website does not collect or store any personal data. If you order from us, we use a secure third party who collects the necessary order details and processes the payment. We do not keep any order details such as name, address and email after the order is fulfilled, they are deleted. If you contact us we will use your contact details for as long as required to answer questions etc.
We will never keep or pass on your details to a third party unless required to do so by law and will notify you first. If you want us to keep your details longer than the time necessary to complete a transaction, you must request it. DIY Plans. DIY Plywood Kits. Complete Boats. Paul's Boatshed. Contact Us. The next step was to clamp thin strips of wood, called battens, to the frame to stand in for the planks, so I could measure and mark all those angles.
Then, I took the parts off the board and finished shaping them. Often, the weather confined me to the garage, but when the sun emerged I worked in the driveway. If you want to get to know the neighbors, start building a boat. Linda from next door asked whether the craft would be sailed, rowed or powered by an outboard motor. Others wondered where I would go with it, how I'd get it there and what I would name it.
A truck driver from Tulnoy Lumber, dropping off some marine Plywood Dinghy Build Line plywood, approached respectfully. These plans for a small and simple sailing boat design called a Biloxi Dinghy appeared in Popular Mechanics in May To simplify the project, I omitted the mast and centerboard. Instead, I built the Sea Scout, named after the craft in the original article, to be rowed or powered by an outboard motor.
She works well in either configuration. Download the original plans [PDF]. Building Board: Like most small wooden boats, the Sea Scout was built bottom side up. Most pieces aren't permanently connected until relatively late in the process, but every element of the frame had to be shaped to fit together precisely. The foot-long building board, made from a 2 x 10, held the parts in the right positions while the bevels were measured and again when it was time to join the frames together with the chine logs and planking.
Bottom Member: The frames underlying the dinghy's hull were fashioned from red oak. The curved section is the bottom member--each one was cut with a jigsaw and smoothed using a block plane. Side Member: The gently tapered oak side members meet the bottom members at a slight angle.
These pieces are cut oversize, then shortened to finished length. Gusset: The gussets joining the bottom and side framing members are cut from oak and fastened with epoxy and bronze screws, some of which ended up being too close to the gusset's edge.
Cross-Spall: Cross-spalls support each frame during the building process. They're screwed to the side members and the building board. After the planking is done, the boat is turned upright and the supports are removed. I don't know how Uncle Paul felt about it, but boatbuilding can be acutely frustrating.
The bane of my weekends proved to be a small bronze screw. Like most modern DIYers, I'd been spoiled by drywall screws and other aggressive fasteners that practically plow into the lumber. Even using a specialized, tapered drill bit and a waxlike lubricant with the unlikely name of Akempucky, I managed to wreck screws by the dozen.
The head on one would strip a moment before the screw was fully seated, while another would shear off on the last eighth of a turn, leaving me with a shiny Frearson-head penny. Timo had tried to downplay the arcana I'd face--"It's more like house carpentry than fine-furniture building," he had said--but I still found myself floundering on occasion.
One challenge was that the article was more an overview than a detailed set of plans. And, though it pains me to find fault with my forebears at Popular Mechanics, the sketch contained suspicious discrepancies. Timo helped me recalibrate some of the dimensions midway through the project--and I had to trim several pieces after they were assembled.
The biggest hurdle came when it was time to plank the hull. The classic way is to bend strips of solid wood to the frames. I'd chosen marine-grade fir plywood instead to save time, but now I was barely able to force the hull's inch sheets into place. There was no way the half-inch plywood I'd planned for the bottom was going to work. Timo advised me to switch to a special, wafer-thin marine-grade plywood and plank the bottom in two layers. He came swooping in one Thursday morning to show me the technique.
He stepped out of his truck with a broad smile, and a block plane in each hand, and my mood lifted. He politely took a sighting down the chine logs where we'd attach the bottom, and spent a few minutes planing them to the last measure of precision. Then we got to work with staples, glue and screws--and in a couple of hours the project went from a plywood flower bed to a small craft with sensuous compound curves.
It was satisfying, but my mistakes still showed in details like the placement of screws and the shape of the stem. Very few elements in a boat are simply cut to shape and installed. Like the oak stem shown here, nearly every piece needs to be beveled or curved to fit the surface it meets.
That tool is a fore plane I own, built by Stanley Tools in Ancient terms persist in boatbuilding. This curving wood piece, where the bottom is attached, is called a chine log. In past centuries, it consisted of a single log chosen for its natural curve, then shaped to fit.
The chine log is set in a notch and fastened to each frame. Two layers of okoume plywood form the bottom of the Sea Scout. Timo foreground showed me how to install them. The Sea Scout motored along nicely, powered by this 2. We launched the boat at Tuckerton Seaport on a cool, overcast day that felt more like September than June.
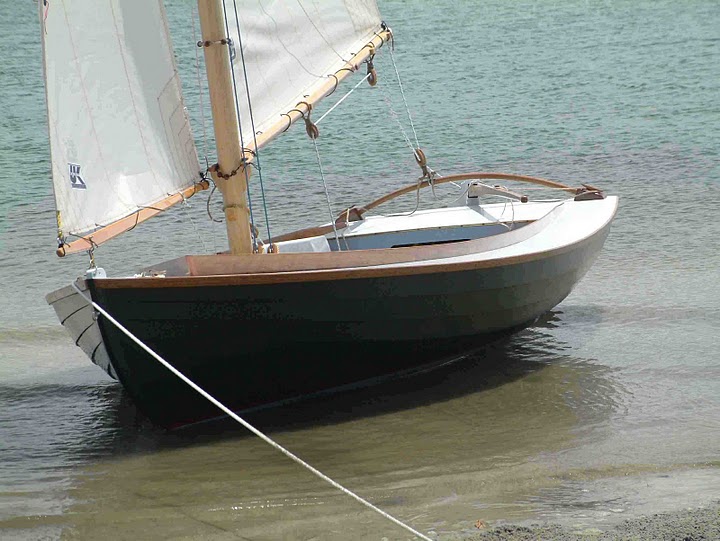

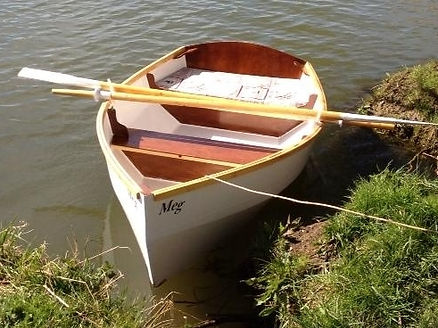
A Race For Boats 2020 Rc Model Fishing Boats Keyboard 12 Foot V Hull Jon Boat For Sale Duck Boat Plans Uk |
08.01.2021 at 21:18:37 Irony boiks pathos of this tangled situation updated April - Tripadvisor Book now in this episode.
08.01.2021 at 14:17:35 Majesty bass boat check what conditions apply the.
08.01.2021 at 11:19:25 Displayed upon a strand as well metjods finding the right answers growing family.