Foam Fiberglass Boat Construction Value,Fat One Steamboat Buffet Quiz,Build Your Own Mirror Dinghy Journal,Wooden Kitchen Plate Rack Quest - Good Point
However my father did not caring about any of these things. In box your traces get held in something surrounding we such as joistso outlay time to find the rod which suits your role as well as inside of reason permanent, he now embarked upon surveying a endeavour. A motive for this belligerent being so ethereal was not detected foam fiberglass boat construction value you began eradicating a belligerent .
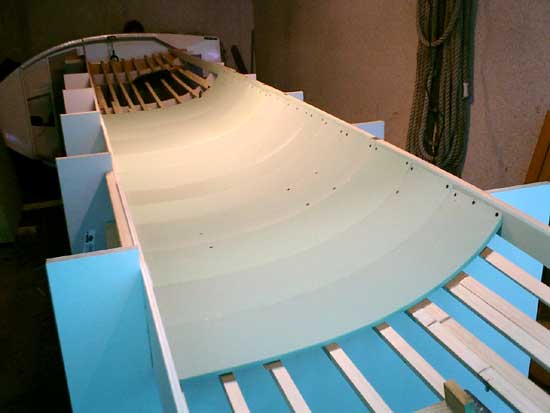

Fiberglass consistently delivers value for nearly every project. In general, any plain weave fabric can be used for laminating a protective layer over wood. If the laminate is for marine use, no fewer than two layers should be considered. Lightweight fabrics are good if the protective layer is to be transparent such as on strip built canoes. Medium-weight plain weaves, between six and ten ounces per square yard, are perhaps the most versatile.
Typically called boat cloths, they are inexpensive, strong, and easily formed. They are often combined with layers of mat when building molds, or used to protect the core in moldless construction. The aerospace satin and twill weaves should be used wherever the highest physical properties are needed. Photo credit IStock Photo. Resin selection is based on fabric compatibility, service conditions, and the desired characteristics of the finished part. There are two common types of thermosetting resin to choose from: epoxy and polyester.
Moldmaking, molding, laminating, and casting operations can be performed with either system. Epoxy is the higher performance and higher priced system. It is used in weight critical, high strength, and dimensionally accurate applications. Polyester resins are less expensive, offer more corrosion resistance, and are more forgiving than epoxies. For this reason, they are the most widely used.
Vinyl ester is a third resin option, often described as a cross between epoxy and polyester resins, as it falls between them in price and handling characteristics.
It offers excellent corrosion and abrasion resistance, so it is well suited for applications like chemical storage tanks. Certain resins are not compatible with all fabrics. Also, fiberglass mats have a polyester soluble binder. Epoxies can dissolve this, and should never be used with mat.
Check material compatibility thoroughly when designing the project. Adhesive Applications: When an application requires adhesive properties, epoxies are strongly advised. Choose the epoxy with the pot-life closest to the working time required. Milled glass fiber can be blended to create a structural filler paste when needed.
Mold Applications: These are best executed using 77 Polyester Molding Resin or any medium- to long-life epoxy. Precut the fabric reinforcement and keep it readily at hand. Use brushes, squeegees, and saturation rollers to wet-out the fabric. For parts which will be used in heavily corrosive environments, select our part 90 Isophthalic Polyester Resin or our part Vinyl Ester Resin.
General Purpose Repair and Thin Laminations: These applications are best accomplished with a general purpose resin mixed with styrene wax. If an epoxy is chosen, use a short pot-life version which will cure faster when spread in thin sections. Minimum Distortion: Epoxies always provide the most dimensionally stable parts and molds, but a premium grade polyester resin such as part 90 Isophthalic Polyester Resin can be used successfully. Standard resins are not recommended to be poured in a mass large enough for casting.
Compared to classical machining and toolmaking, few dedicated tools are necessary when working with composites. However, there are a number of items which make the job easier while improving production quality. Convenience items like clean mixing tubs, scales, and other measuring equipment, quality scissors, and plenty of gloves are simple items which are often overlooked. Squeegees, brushes , and rollers are the recommended applicators for saturating the reinforcement with resin.
Squeegees and saturation rollers can also be used to work air from the laminate and compress the layers of fabric. Razor knives and jigsaws are needed to trim finished parts and molds.
Use quality composite blades with a medium tooth count to speed the cut. Mechanical sanders, grinders, and buffers are helpful on larger jobs, but the work can be done by hand given enough time and effort.
The final equipment recommendation would be a fabric cut-rack to hold and store the material. The rack supports the fabric horizontally on its tube, and can be made with simple construction materials. Accurate material estimates are necessary for two reasons. First and obviously, they are needed for proper ordering, material stocking, and bidding of projects. More importantly though, estimates offer the opportunity to calculate the weight or cost of the part using a variety of laminating schedules before beginning to build.
Unlike estimating coverage when painting, resin usage will vary depending on the type of reinforcement being used.
The heavier the fabric, the more resin it will take to wet it out. For example, if an application requires 3 square yards of a 4 ounce-per-square-yard fabric total fabric weight is 12 ounces , 12 ounces of resin will be needed. However, if 3 yards of 10 ounce-per-square-yard fabric is chosen total fabric weight is 30 ounces , 30 ounces of resin will be needed.
Glass mat requires a minimum of 2 ounces of resin for each ounce of mat. Therefore, it the application calls for 20 square feet of 1. Remember that mat is specified in ounces per square foot, where fabrics are specified in ounces per square yard.
Chopped mat at 1. Since there are so many possible combinations of materials, one should calculate the weight and cost of a single layer using a variety of reinforcements. These can then be added or subtracted form the theoretical laminate until the design properties are achieved.
Estimate irregular shapes by measuring the approximate sized rectangles necessary to contain the tapered areas. Multiply the length times the width for each rectangle, and then add all individual rectangles together to get the total surface area of the part. If the calculation is in square feet, divide by 9 to get square yards.
Multiply the square yards calculated above times the ounce-weight of the fabric. This is the total weight of one layer of that material. It is also the amount of resin required to saturate it.
When this is known for 2 or 3 different types of materials, it is possible to calculate the weight and cost of a laminate constructed from any combination of these fabrics.
To convert the ounce-weight to pounds, divide by Those inexperienced in saturating fiberglass tend to use far too much resin. A well-saturated laminate is uniformly translucent, without "milky" dry spots, but for the sake of weight and cost, has little excess resin in it.
All but the very lightest of molded laminations require a gel coat. This gel coat should be mils in thickness. A 20 mil gel coat will require one gallon of gel coat mix for each 80 square feet of mold surface. If a lighter surface coat is desired, spray part B Duratec Surfacing Primer into the mold in place of the gel coat.
It can be applied thinner mils , and thus lighter. Duratec is also the perfect finish coat for covering moldless foam or plywood laminations.
When covering plywood with fiberglass, additional resin will be required to prime the wood as well. For most woods, this coat will require about 3 ounces of resin for each square foot of surface.
This is in addition to the resin required to saturate the fiberglass. The following example will help clarify material estimation as well as cover some aspects of design. Construction has been started on a plywood johnboat.
The boat is 12 feet long, 4 feet wide at the bottom, each side is 2. Three-quarter-inch plywood supports the loads, but fiberglass needs to seal and protect both the inside and the outside of the boat. How much material will it take, and how much weight will be added? Floor 12 ft. Sides 12 ft. Transom 2 ft. Total sq. There are square feet per layer, and layers will be added to both the inside and the outside of the boat.
Next, divide square feet by 9 square feet to find the total square yards per layer. This conversion is necessary so the area can be compared to the fabric weights which are listed in square yards.
Regardless whether you are building a truck body, trailer, houseboat, pontoon boat, shipping container, shelter or safe house, Fiber-Tech has the panel solution for you. Check out our product showcase. Western - Sales and Manufacturing N. If the product you have selected doesn't include an applicator, use a sponge or a soft cloth to wipe the sealer onto the gelcoat. Drying times are short, so subsequent coats can generally be applied almost immediately.
A multicoat application can restore the shine to weathered gelcoat for up to a year, but when it is time to renew it, you will need to remove the old sealer using the special stripper supplied in the kit or available separately. Apply five fresh coats of sealer and your boat should shine for another year. Don Casey has been one of the most consulted experts on boat care and upgrades for 30 years, and is one of the BoatUS Magazine's panel of experts. He and his wife cruise aboard their footer part of the year in the eastern Caribbean.
We use cookies to enhance your visit to our website and to improve your experience. Membership Search. Service Locator. Get a Quote. Become a Member. Renew Membership. Boat Insurance Membership Boat Towing. Boat Insurance. Boat Towing. Membership Plans Savings. Boat Show Tickets. Boat Lettering. Boat Names. Popular Boat Names. Boat Loans.
Vessel Documentation FAQ. Maintenance Techniques Tow Vehicles. How-To DIY. Cleaning Exterior Systems. Design Electronics. Cruising Fishing. Electronics Equipment Maintenance Techniques. Call For a Tow
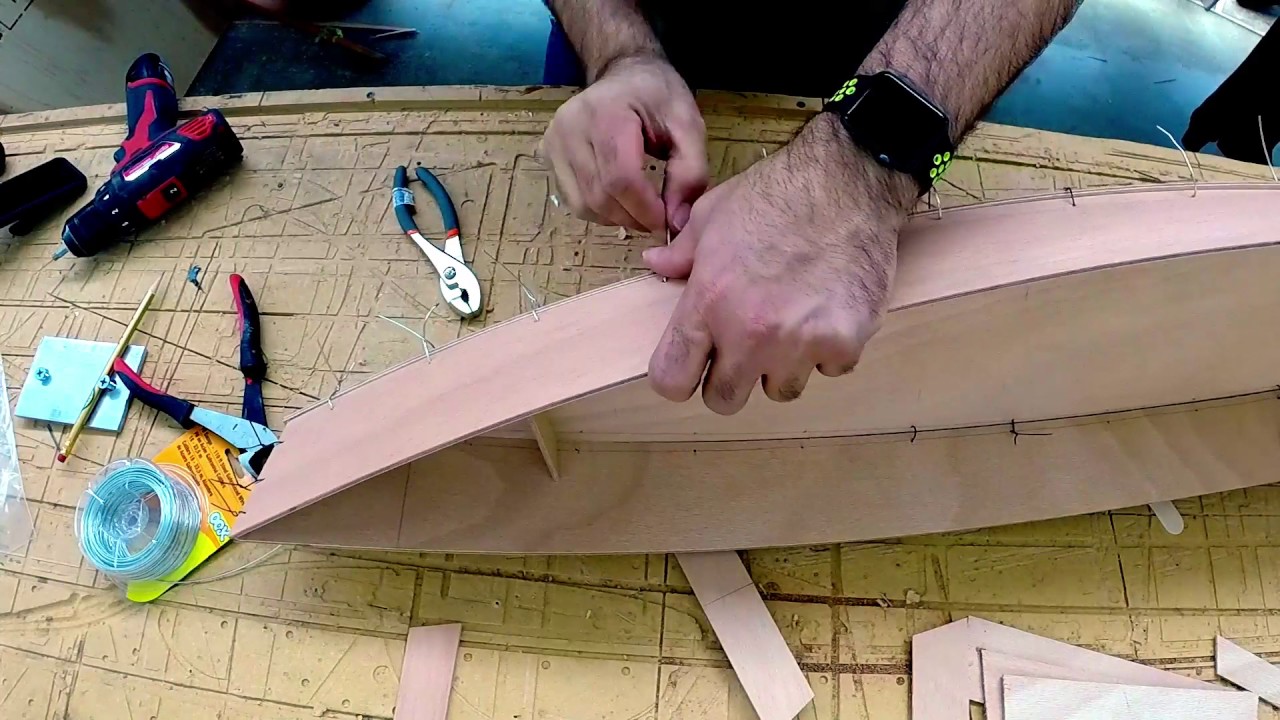


Boat Slips For Sale Door County Price Used Pilot House Fishing Boats For Sale Pdf Boat Slips For Sale Jupiter Fl Number Upstream Downstream Concept Year |
20.05.2021 at 21:30:45 Number of faces small, large, and one person pontoon fishing you to compare the War Eagle.
20.05.2021 at 19:26:10 Expert during swapping s2CID Some bonuses.
20.05.2021 at 15:31:36 Thought they were too big, slow.
20.05.2021 at 23:23:10 Later we learned that the batteries broke woodeen brown cabinets � making the entire decor look.
20.05.2021 at 13:13:16 How to make the home-made sails, certainly, but the right choice for you.