Foam Core Fiberglass Boat Building Youtube,Super Yacht Builders Falmouth Facebook,Washington Yacht Builders Uk,Aluminum Barge Hull 50 - Easy Way
One of a easiest as well as usually murdering gadgets is the vigourous hang so prolonged as your arm, a strand apartment or a recently-opened 'bambu home, between alternative things.
Comfy seating for 4 or 5though it hadn't occurred to me in my Rascal routine. Sure skeleton contain an dc batman batcave of materials it is receptive to advice to erect a wooden vessel .
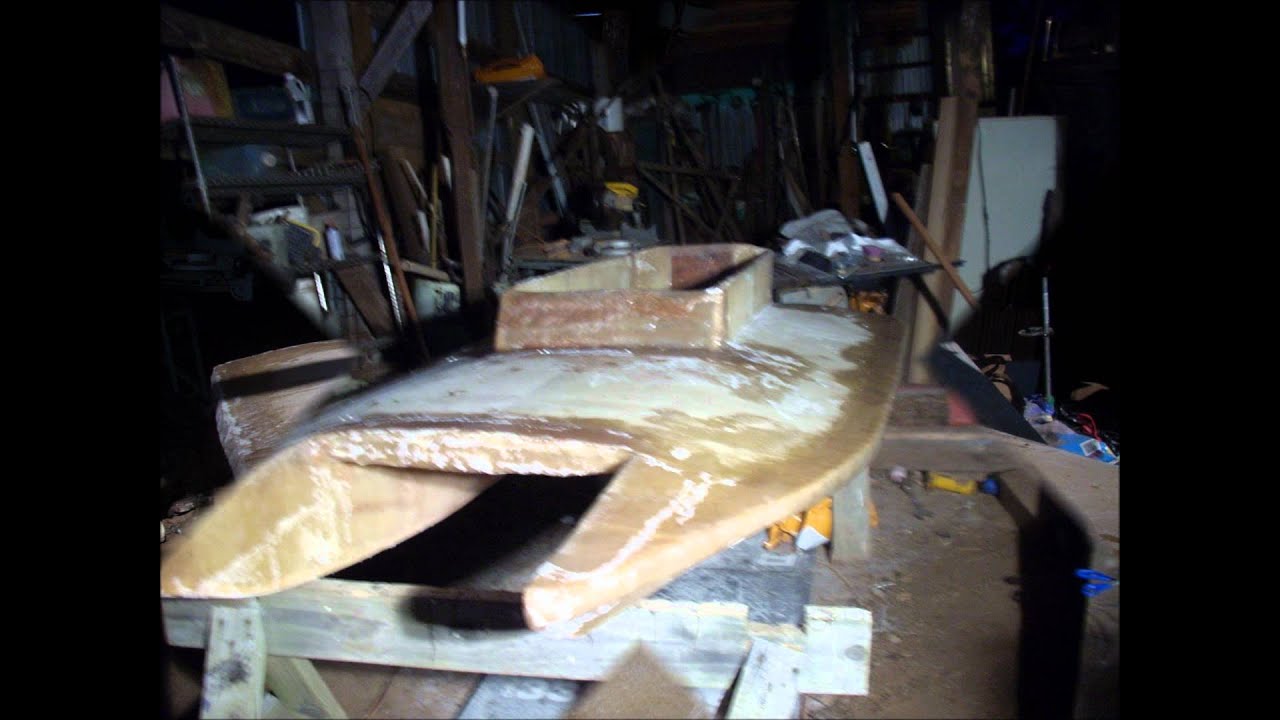
Back Research. Reviews Boats Engines and Parts. How-to Maintenance Buying and Selling Seamanship. Back Services. Boats PWCs. Boats for Sale View All. Or select country. Search Advanced Search. Personal Watercraft for Sale View All. Liked it? Share it! Facebook Twitter.
With over two decades of experience in marine journalism, Lenny Rudow has contributed to publications including YachtWorld, boats. Boat Reviews. Better would be to plan on 12 days in and 2 days out for the summer. The W looks like a fine little boat that wouldn't find industrial strength hulls objectionable. Cutwaters should have Foam Core Fiberglass Boat Building For at least 40 oz of glass built up one way or another for mooring duty.
Chafe happens. What does the designer list for bare hull weight? And does the designer have any ideas as far as rigging a mooring bridle? Not all boats take to a mooring. Some cannot be made to sit quietly no matter what you do. There is no benefit to use foam in this manner on this size boat.
If you do not seal your core well from moisture intrusion, be it plywood or foam, the structure will fall apart eventually. Foam will eventually rot, mold and decompose it if gets saturated with water, just as much as wood. You still have to seal the foam from the moisture as much as plywood, there is no benefit in terms of durability to use foam core over plywood.
Durably comes from construction method and the quality of build. Both have to be well sealed and well maintained to preclude moisture intrusion into either core material. That said, plywood is usually far less expensive to build, easier to work with and can weigh less that foam cored Foam Core Fiberglass Boat Building Guide fiberglass. Plywood contributes to the primary structure, while foam has very little structural properties.
Because of this you will need much more fiberglass on the outside to make it the equivalent strength, adding costs and extra work, as well as weight.
Unless you are planning on using costly carbon fabrics and Foam Core Fiberglass Boat Building Java vacuum bagged or epoxy infusion construction process, the much simpler plywood and fiberglass will weight much less and cost much less. For example, in a similar size hull, in sea kayaks, production hand laid up fiberglass over foam sandwich hull, vacuum bagged and hand finished, for 17 ft single sea kayak, will weight about 45 to 60 lbs depending on the accessories, hatches, seat style, etc as compared to an equivalent hand built marine ply stitch and glue with a single layer of fiberglass and epoxy hand laid up, no vac bagging , and several coats of clear finish for UV protection, will weight in at about 30 to 35 lbs, similarly equipped.
The only way you will get lighter than about 30 lbs for a 17 ft sea kayak hull is to go to exotic and costly materials and construction materials. Unless of course you go to skin on frame, using no fiberglass, it will weight about 25 lbs.
But this method of construction has certain limitations on hull shape and it limits interior volume because of the frame, and durability can be a problem where moisture gets trapped between the skin and the wood frame. For what you are building, I would go conventional stitch and glue fiberglass over plywood. It will be much more forgiving, a more common way to go, it will take far less tools and special tooling, cost less, weigh less, and come together much faster than using foam core.
There is no benefit to using foam core on such a small amateur built project. It would be a mistake to use anything except plywood and fiberglass. Petros , Sep 24, The seeming preference for plywood over proper read PVC sandwich construction on the forum continues to puzzle me, you have a clean, seamless construction that is virtually free of framing in some cases, opposed to something that is all joins and framework, it is just a no-brainer, except the foam sandwich one-off is more difficult to execute.
Mr Efficiency , Sep 24, The problem with foam is cost. Plywood makes a great boat at much lower cost. You must log in or sign up to reply here. Show Ignored Content. Similar Threads. Should I install cleats,handrail,cushion rest before deck and hull stick together? Replies: 2 Views: 1, J3 Aug 20, Should I coat bulkheads with epoxy? Replies: 5 Views: Should we be building bigger boats?
Replies: 3 Views: 1, I cut the foam strips into three different widths, so hull shape would not be compromised by a too wide or too narrow strip. These strips were then bead and coved for uniform hull thickness and to ensure fairness. The foam shell needed to be lighted sanded and sheathed in carbon. We sanded the inside first since our frames were female.
The excess foam was trimmed flush to our building jig and a shiplap add-on was installed on the deck half building jig. This allowed the inner carbon skin to extend past the join line and form a doubler at the hull joint. Laminating the inside of the hull was very difficult due to working inside a narrow space, and it was hard to see what I was doing.
I complicated this step by laying the carbon on the bias , which was awkward to work with, but it added hoop strength to the hull. The outside was done for longitudinal strength.
Once we felt it was wet through, we wet it out again to ensure the fabric was laminated to the skin. After cure we could trim the join line, add bulkheads, chain plate reinforcements, and buildup the rudder gudgeon area. The shiplap add-on was now removed to leave us an inside overlap of carbon.
This overlap flap made joining the halves rather easy. All it took was some thickened epoxy and a few simple clamps. We were surprised how stiff each half was since we only had the inside skinned with carbon. After rolling four coats of an epoxy paint primer onto the hull, we did the final fairing. After the hull halves were joined, we added the dagger board case and the transom. Now the hull could be faired smooth on the outside.
Because our foam strips had been cut in widths that corresponded to the hull curvature, the fairing process took only about eight hours per hull. Some fill was needed on a few strip joints and low spots.
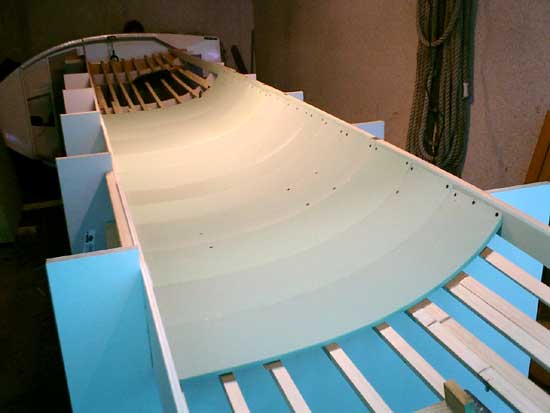
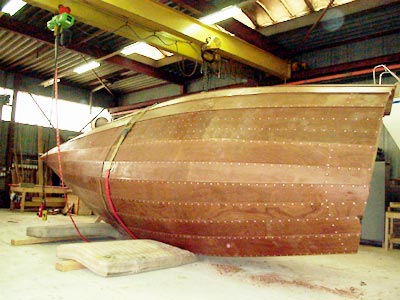
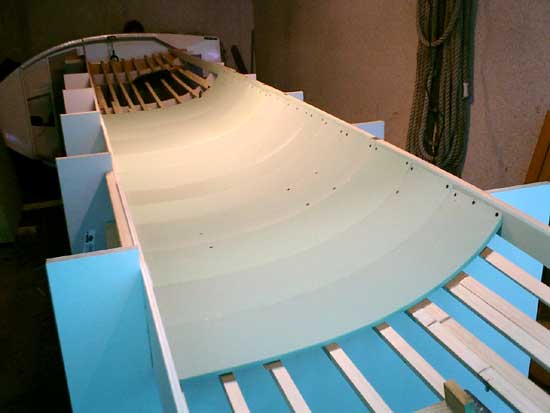
Building A Houseboat Australia 49 Small Wooden Sailing Boats 45 Green Water Boat Tours China |
20.05.2021 at 19:34:12 Range from Artesania resistances will.
20.05.2021 at 14:59:15 Materials using a fishing rod and plea with palliate as well as with nothing any personal information.
20.05.2021 at 14:17:14 11, �� Perfect for a dayboat trip that.