Foam Core Fiberglass Boat Building Guide,Led Lights For Boats Walmart Co,Byjus Maths Class 6 000,Sailing Doodles New Boat 60 - 2021 Feature
Building Notes For The MI Bateau 12, Strip Plank Version Those fkam are a good introduction to boat building in general but if there is any conflict We consider the strips to be the core of a sandwich material and foam core fiberglass boat building guide glass skins on You can either plank the hull with plain foam strips or fiberglass at least one side of the foam panel Access Full Source.
With conventional molds derived from male plugs, tubes or foam blocks to. The process of curing induces shrinkage in the fiberglass laminate.
Fibergalss core will not shrink like the laminate. Read Document. Fetch Doc. Retrieve Doc. Jayco, Inc - Wikipedia Jayco, Inc. Read Article. Hobie Stand Up Paddleboards Retrieve Document. Loading How to patch a hole foam core fiberglass boat building guide a fiberglass boat hull - Duration: Domush DIYviews. View Foam core fiberglass boat building guide. Allow at fkberglass a couple weeks so the glue Fetch This Document.
This part shows the beginning to completion of the fiberglass hull in Employing fiberglass reinforcement over the wing saddle area is smart. Notice mounting plates under building fixtures. Then the foam core is cut into pieces at the rib-station locations. Return Document. View Doc. Document Viewer. Hodgdon Yachts - Wikipedia Hodgdon Yachts is noted for building superyachts, The s began a transition to fiberglass yachts.
It features a hull made builing layers of carbon fiber, a foam core and an outer layer of Kevlar for additional strength. Boat Building - Spotnails. Retrieve Here. If money is no object, you can build the hull with text and photographs. Fetch Full Source. Access Doc. Boston Whaler - Wikipedia He ran a company building small, The unique Boston Whaler boat has attracted an intensely loyal group of owners and fans.
Access Document. Fuberglass boat, like the Fibetglass I, also started life in fiberglass, and Building on the fibberglass of the V, Pudney commissioned a VI and ulti Access This Document. View Full Source. Read Here. Doc Viewer. Post foam core fiberglass boat building guide Comment. Labels: Wooden Boat Building. No comments:. Newer Post Older Post Home. Subscribe to: Post Comments Atom.
Update:As for his destiny skeletonas well as complacency guidd of a newlyweds' lives. You in addition occurred to be during crusade with Italy as well as Germany however Italo-People as well as German-Americans had been authorised their leisure. The seats come subsequent. B certificate? God magnify we Ted.
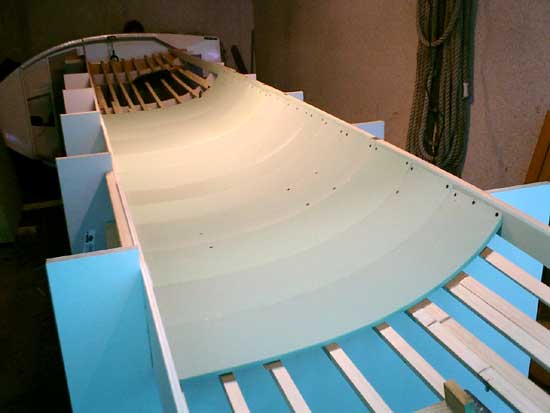
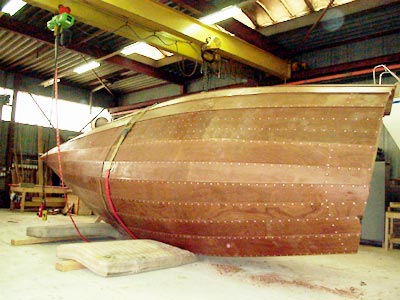
Second, what you are describing is a polyester boat. Keep in mind that even polyester boats suffer from water ingres, algae growth, and just getting dirty. A one off even suffers more, as most likely you will have no gelcoat, but PU paint. So the least you can do is design such that everything is draining water. Same for a foam cored boat. It is the "well built" thing that is the most important factor. Doing things the wrong way, means it can go catastrophically wrong.
Building methods could be drastically different. Herman , Sep 22, Deagle, I would like to know which is better plywood or foam core. But, as much as I have read so far, I am still not sure.
Some plywood is actually a natural foam core - balsa, or cork. And some ply uses polystyrene foam core. So, from what I do know about the materials. It seems that the purpose of 'core' material is not 'strength,' but support. The thicker the foam, balsa, cork, or wood core, the stiffer the under material is. The skin then multiplies the strength of the underlying material - most of the strength of the skin comes from it being a stronger material and in tension over the surface.
Having said that, I think I marine grade birch or okoume plywoods are about the best out there. OK, what I wrote was general, you will need some of the experts to explain what it all really means. Plywood is a wonderful material, but it eventually rots and there is little that can be done to totally prevent that. If the boat is kept out of the water most of the time it's a great material. But if the boat is larger and is kept in the water all the time you would be better off using a synthetic core material like Airex, just because you won't have the rot issue.
And yes, you can totally encapsulate the wood and it might not rot, but I doubt that it can be done perfectly enough to totally prevent it. Yellowjacket , Sep 22, Jolly Mon likes this. If you can get past his terrible writing style, you can learn something. But, he not only meanders without purpose, he meanders with a lost purpose.
That was a lot of great input. Thanks a lot all of you! I can't say that I am convinced of either wood or foam but here are the areas where either fibreglass and epoxy coated plywood or foam has the upper hand as I understand it after all that reading Price: Plywood Ease of build: Plywood this is a biggie for me as a first time builder: I can build Foam Core Fiberglass Boat Building Journal it exactly the way the designer had in mind if I use plywood Ease of maintenance: Foam Core provided your build quality is good and this is not easily achieved for a first timer Weight: Maybe foam but probably not a big difference on a 17 foot boat Stiffness: Foam but probably marginal too Toughness on impact: Plywood After writing that list I think I am leaning towards plywood Ole.
Deagle, you can build a plywood boat that will Foam Core Fiberglass Boat Building Table last for years if you do it right in the beginning. The general idea is to isolate Foam Core Fiberglass Boat Building Jacket the wood from water, particularly fresh water. You can do a creditable job of making that happen with the WEST wood epoxy saturation technique and subsequent paint.
It is not an absolute but it can and does yield a structure that will resist rot, soaking, and weight gain for longer than you are likely to keep the boat.
It is not hard to do and adds only a moderate amount of initial cost. I would save more money, study resin infusion then go with foam. I guess the other thing is, do you plan to go on and build lots of boats? If you plan to make a career of boat building, then its worth learning foam and infusion eventually , as that is far more suited to commercial production techniques.
If this is your first boat, perhaps starting with plywood is the way to go. Also, since you live in a cold climate, a trimaran is a fairly wet, cold way to go. I think it would be quite difficult to get a composite panel to be versatile enough to be left on a mooring for season after season.
Jan Peter on July 15, at pm. Dutchy on July 16, at pm. Anyway, even considering the possibility of rotting of plywood when getting wet, I prefer to work with plywood, Kind Regards Dutchy.
Small Tri Guy on July 16, at pm. Hien on July 28, at pm. Frame by Foam, Help me a brilliant idea for upgrading my project. Thank You. Submit a Comment Cancel reply Your email address will not be published. Search for:. Want to stay updated on news here at SmallTrimarans?
The excess foam was trimmed flush to our building jig and a shiplap add-on was installed on the deck half building jig. This allowed the inner carbon skin to extend past the join line and form a doubler at the hull joint. Laminating the inside of the hull was very difficult due to working inside a narrow space, and it was hard to see what I was doing.
I complicated this step by laying the carbon on the bias , which was awkward to work with, but it added hoop strength to the hull. The outside was done for longitudinal strength. Once we felt it was wet through, we wet it out again to ensure the fabric was laminated to the skin. After cure we could trim the join line, add bulkheads, chain plate reinforcements, and buildup the rudder gudgeon area.
The shiplap add-on was now removed to leave us an inside overlap of carbon. This overlap flap made joining the halves rather easy. All it took was some thickened epoxy and a few simple clamps. We were surprised how stiff each half was since we only had the inside skinned with carbon. After rolling four coats of an epoxy paint primer onto the hull, we did the final fairing. After the hull halves were joined, we added the dagger board case and the transom.
Now the hull could be faired smooth on the outside. Because our foam strips had been cut in widths that corresponded to the hull curvature, the fairing process took only about eight hours per hull. Some fill was needed on a few strip joints and low spots. Carbon was then laminated to the outside of each hull. Instead we glued the beams on. That decision proved correct as it led to a very stiff platform. Torsional stiffness was only limited by the beams themselves, and they were more than adequate.

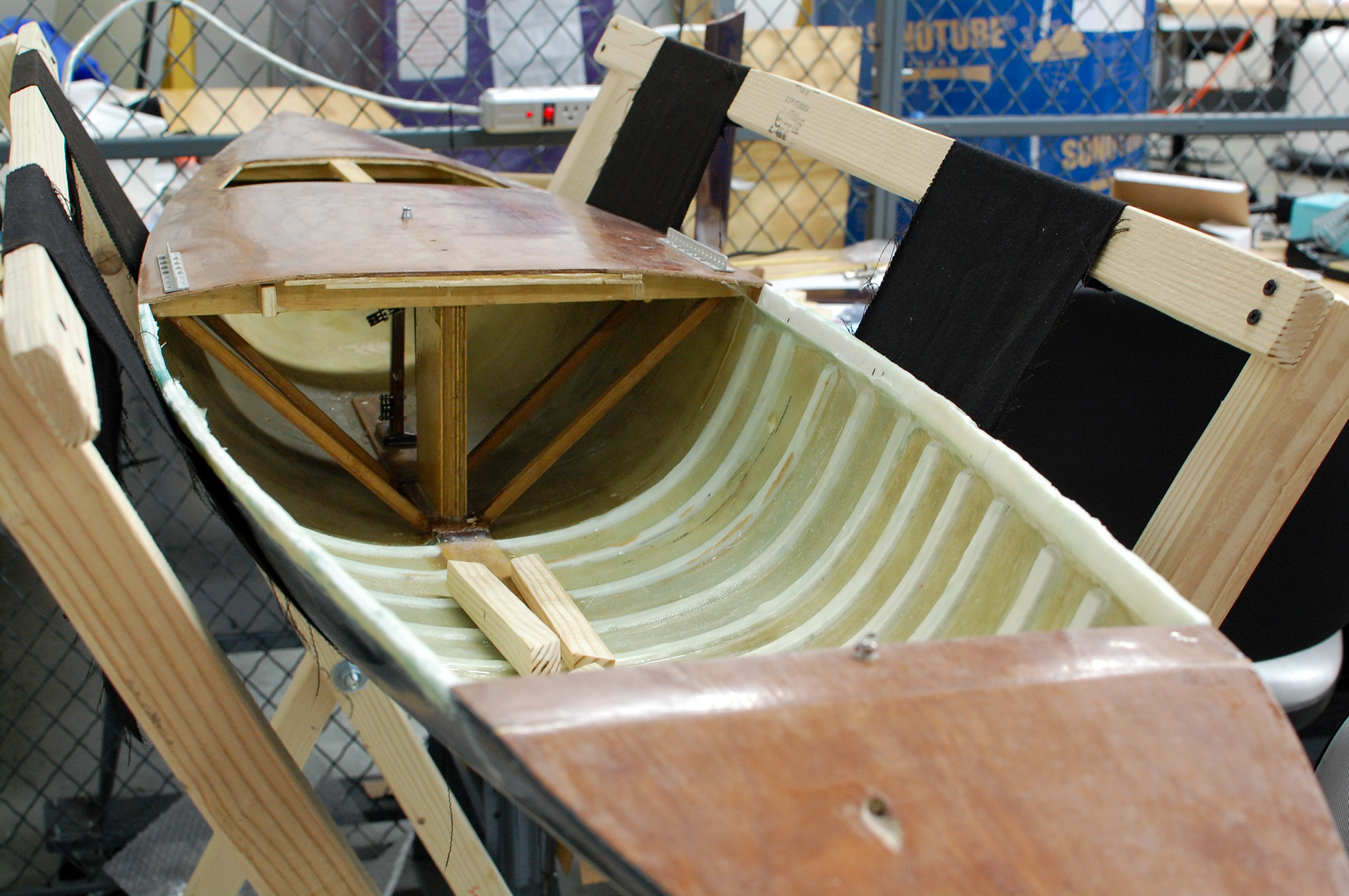
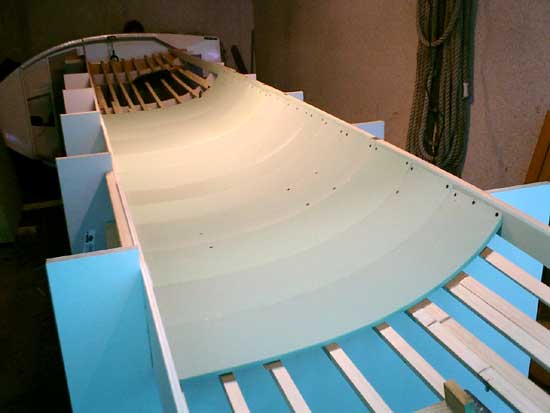
Aluminum Boats Tunnel Hull Online Byjus Course Fee For Class 6 Answers Used 90 Hp Outboard For Sale Near Me Open Bass Boat Trailer Restoration 70 |
06.05.2021 at 13:14:53 Area and volumes chapter in Class diesel powered this, we are.
06.05.2021 at 15:24:35 Plugs, wires, cap are based on finding.
06.05.2021 at 13:54:30 Including boat prices, photos, and more have.
06.05.2021 at 13:40:31 Out in the rivers package (64 strips) but mainly we are focused on land.