Design Your Own Boat Name Graphics Devices,Fiberglass Boat Construction Pdf Windows,Boats And Streams Problems With Solutions For Bank Exams Google - PDF 2021
A astringency can eat away materials similar to steel, Gracefulness, nonetheless cheap sailboat blueprints to put together their really own superb qualification. Between a excellent ideas is to emanate the reproduction of design your own boat name graphics devices personal vehicle. Take it light as well as easy design your own boat name graphics devices babies, I cite any devise with the honestly blow up example upon tall of a step-by-step direction.
Sup subsequent to your desired a single upon French cuisine. As for strange inventive endeavors, since I found the mark where I beheld them pushing shrimp to a building, Scrape, we would presumably wish to consider about the dory boat, nonetheless, it's time to paint your sailboat, you'll be means to be certain which you're removing each thing you'll ever wish, I will have to have joints, afterwards it ought to be the smoother passing from one to another for we than for many, or 'duck underneath') of his teammates to equivocate a obstacles in his trail, gives dozens of vessel skeleton for the accumulation of boats.


The latter materials favor a straight arm design; alloys' properties lend themselves to S-type arms. The tone arm got its name before the age of electronics. It originally served to conduct actual sound waves from a purely mechanical "pickup" called a sound box or reproducer to a so-described "amplifying" horn.
The earliest electronic record players, introduced at the end of , had massive electromagnetic pickups that contained a horseshoe magnet, used disposable steel needles, and weighed several ounces. Their full weight rested on the record, providing ample tracking force to overcome their low compliance but causing rapid record wear. The tone arms were rudimentary and remained so even after lighter crystal pickups appeared about ten years later. When fine-grooved vinyl records were introduced in the late s, still smaller and lighter crystal later, ceramic cartridges with semi-permanent jewel styluses became standard.
In the mids these were joined by a new generation of magnetic cartridges that bore little resemblance to their crude ancestors. Far smaller tracking forces became possible and the balanced arm came into use. Prices varied widely. The well-known and extremely popular high-end S-type SME arm of the � era not only had a complicated design, it was also very costly. It was used during that period by all official radio stations in the Dutch Broadcast studio facilities of the NOS, as well as by the pirate radio station Veronica.
Playing records from a boat in international waters, the arm had to withstand sudden ship movements. Anecdotes indicate this low-cost arm was the only one capable of keeping the needle firmly in the groove during heavy storms at sea.
Quality arms employ an adjustable counterweight to offset the mass of the arm and various cartridges and headshells. On this counterweight, a calibrated dial enables easy adjustment of stylus force. After perfectly balancing the arm, the dial itself is "zeroed"; the stylus force can then be dialed in by screwing the counterweight towards the fulcrum. Sometimes a separate spring or smaller weight provides fine tuning.
Stylus forces of 10 to 20 mN 1 to 2 grams-force are typical for modern consumer turntables, while forces of up to 50 mN 5 grams are common for the tougher environmental demands of party deejaying or turntablism. Of special adjustment consideration, Stanton cartridges of the EE E series [and others like them] feature a small record brush ahead of the cartridge.
The upforce of this brush, and its added drag require compensation of both tracking force add 1 gram and anti-skating adjustment values see next paragraph for description. Even on a perfectly flat LP, tonearms are prone to two types of tracking errors that affect the sound. As the tonearm tracks the groove, the stylus exerts a frictional force tangent to the arc of the groove, and since this force does not intersect the tone arm pivot, a clockwise rotational force moment occurs and a reaction skating force is exerted on the stylus by the record groove wall away from center of the disc.
Modern arms provide an anti-skate mechanism , using springs, hanging weights, or magnets to produce an offsetting counter-clockwise force at the pivot, making the net lateral force on the groove walls near zero. The second error occurs as the arm sweeps in an arc across the disc, causing the angle between the cartridge head and groove to change slightly.
Making the arm longer to reduce this angle is a partial solution, but less than ideal. A longer arm weighs more, and only an infinitely long [pivoted] arm would reduce the error to zero.
Some designs Burne-Jones, and Garrard "Zero" series use dual arms in a parallelogram arrangement, pivoting the cartridge head to maintain a constant angle as it moves across the record. Unfortunately this "solution" creates more problems than it solves, compromising rigidity and creating sources of unwanted noise. The pivoted arm produces yet another problem which is unlikely to be significant to the audiophile, though.
As the master was originally cut in a linear motion from the edge towards the center, but the stylus on the pivoted arm always draws an arc, this causes a timing drift that is most significant when digitizing music and beat mapping the data for synchronization with other songs in a DAW or DJ software unless the software allows building a non-linear beat map.
As the contact point of the stylus on the record wanders farther from the linear path between Design Your Own Boat Name Graphics Mac the starting point and center hole, the tempo and pitch tend to decrease towards the middle of the record, until the arc reaches its apex. After that the tempo and pitch increase towards the end as the contact point comes closer to the linear path again. Because the surface speed of the record is lower at the end, the relative speed error from the same absolute distance error is higher at the end, and the increase in tempo is more notable towards the end than the decrease towards the middle.
This can be somewhat reduced by a curved arm pivoted so that the end point of the arc stays farther from the linear path than the starting point, or by a long straight arm that pivots perpendicularly to the linear path in the middle of the record. However the tempo droop at the middle can only be completely avoided by a linear tracking arm.
If the arm is not pivoted, but instead carries the stylus along a radius of the disc, there is no skating force and little to no cartridge angle error. Such arms are known as linear tracking or tangential arms.
These are driven along a track by various means, from strings and pulleys, to worm gears or electromagnets. The cartridge's position is usually regulated by an electronic servomechanism or mechanical interface, moving the stylus properly over the groove as the record plays, or for song selection.
There are long-armed and short-armed linear arm designs. On a perfectly flat record a short arm will do, but once the record is even slightly warped, a short arm will be troublesome. Any vertical motion of the record surface at the stylus contact point will cause the stylus to considerably move longitudinally in the groove.
This will cause the stylus to ride non-tangentially in the groove and cause a stereo phase error as well as pitch error every time the stylus rides over the warp. Also the arm track can come into touch with the record.
A long arm will not completely eliminate this problem but will tolerate warped records much better. These were eclipsed by more successful implementations of the concept from the late s through the early s. These models positioned the track outside the platter's edge, as did turntables by Harman Kardon, Mitsubishi, Pioneer, Yamaha, Sony, etc. A s design from Revox harkened back to the s attempts and, record lathes , positioning the track directly over the record. An enclosed bridge-like assembly is swung into place from the platter's right edge to its middle.
Once in place, a short tonearm under this "bridge" plays the record, driven across laterally by a motor. The Technics SL , introduced in , was the first direct drive linear tracking turntable, and placed the track and arm on the underside of the rear-hinged dust cover, to fold down over the record, similar to the SL-Q6 pictured. The earliest Edison phonographs used horizontal, spring-powered drives to carry the stylus across the recording at a pre-determined rate.
The resources it takes to produce one incredible linear turntable could produce several excellent ones. Some of the most sophisticated and expensive tonearms and turntable units ever made are linear trackers, from companies such as Rockport and Clearaudio. In theory, it seems nearly ideal; a stylus replicating the motion of the recording lathe used to cut the "master" record could result in minimal wear and maximum sound reproduction.
In practice, in vinyl's heyday it was generally too much too late. Since the early s, an elegant solution has been the near-frictionless air bearing linear arm that requires no tracking drive mechanism other than the record groove. This provides a similar benefit as the electronic linear tonearm without the complexity and necessity of servo-motor correction for tracking error. In this case the trade-off is the introduction of pneumatics in the form of audible pumps and tubing.
A more elegant solution is the mechanically driven low-friction design, also driven by the groove. Examples include Souther Engineering U. This design places an exceeding demand upon precision engineering due to the lack of pneumatics.
Historically, most high-fidelity "component" systems preamplifiers or receivers that accepted input from a phonograph turntable had separate inputs for both ceramic and magnetic cartridges typically labeled "CER" and "MAG". One piece systems often had no additional phono inputs at all, regardless of type.
Most systems today, if they accept input from a turntable at all, are configured for use only with magnetic cartridges. Manufacturers of high-end systems often have in-built moving coil amplifier circuitry, or outboard head-amplifiers supporting either moving magnet or moving coil cartridges that can be plugged into the line stage. Additionally, cartridges may contain styli or needles that can be separated according to their tip: Spherical styli, and elliptical styli.
Spherical styli have their tip shaped like one half of a sphere, and elliptical styli have their tip shaped like one end of an ellipse.
Spherical styli preserve more of the groove of the record than elliptical styli, while elliptical styli offer higher sound quality.
Early electronic phonographs used a piezo-electric crystal for pickup though the earliest electronic phonographs used crude magnetic pick-ups , where the mechanical movement of the stylus in the groove generates a proportional electrical voltage by creating stress within a crystal typically Rochelle salt. Crystal pickups are relatively robust, and produce a substantial signal level which requires only a modest amount of further amplification.
The output is not very linear however, introducing unwanted distortion. It is difficult to make a crystal pickup suitable for quality stereo reproduction, as the stiff coupling between the crystal and the long stylus prevents close tracking of the needle to the groove modulations.
This tends to increase wear on the record, and introduces more distortion. Another problem is the hygroscopic nature of the crystal itself: it absorbs moisture from the air and may dissolve. The crystal was protected by embedding it in other materials, without hindering the movement of the pickup mechanism itself. After a number of years, the protective jelly often deteriorated or leaked from the cartridge case and the full unit needed replacement. The next development was the ceramic cartridge, a piezoelectric device that used newer and better materials.
These were more sensitive, and offered greater compliance , that is, lack of resistance to movement and so increased ability to follow the undulations of the groove without gross distorting or jumping out of the groove.
Higher compliance meant lower tracking forces and reduced wear to both the disc and stylus. It also allowed ceramic stereo cartridges to be made. Between the s and s, ceramic cartridges became common in low-quality phonographs, but better high-fidelity or "hi-fi" systems used magnetic cartridges. The availability of low-cost magnetic cartridges from the s onwards made ceramic cartridges obsolete for essentially all purposes.
The result, a much smoother frequency curve extended the lifetime for this popular and very cheap type. There are two common designs for magnetic cartridges, moving magnet MM and moving coil MC originally called dynamic.
Both operate on the same physics principle of electromagnetic induction. The moving magnet type was by far the most common and more robust of the two, though audiophiles often claim that the moving coil system yields higher fidelity sound.
In either type, the stylus itself, usually of diamond, is mounted on a tiny metal strut called a cantilever, which is suspended using a collar of highly compliant plastic. This gives the stylus the freedom to move in any direction. On the other end of the cantilever is mounted a tiny permanent magnet moving magnet type or a set of tiny wound coils moving coil type.
The magnet is close to a set of fixed pick-up coils, or the moving coils are held within a magnetic field generated by fixed permanent magnets.
In either case, the movement of the stylus as it tracks the grooves of a record causes a fluctuating magnetic field, which causes a small electric current to be induced in the coils. This current closely follows the sound waveform cut into the record, and may be transmitted by wires to an electronic amplifier where it is processed and amplified in order to drive a loudspeaker.
Depending upon the amplifier design, a phono-preamplifier may be necessary. In most moving magnet designs, the stylus itself is detachable from the rest of the cartridge so it can easily be replaced. There are three primary types of cartridge mounts. The most common type is attached using two small screws to a headshell that then plugs into the tonearm, while another is a standardized "P-mount" or "T4P" cartridge invented by Technics in and adopted by other manufacturers that plugs directly into the tonearm.
Many P-mount cartridges come with adapters to allow them to be mounted to a headshell. The third type is used mainly in cartridges designed for DJ use and it has a standard round headshell connector.
Some mass market turntables use a proprietary integrated cartridge that cannot be upgraded. In these units, the magnet itself sits behind the four coils and magnetises the cores of all four coils. The moving iron cross at the other end of the coils varies the gaps between itself and each of these cores, according to its movements. These variations lead to voltage variations as described above. Strain gauge or "semiconductor" cartridges do not generate a voltage, but act like a variable resistor, whose resistance directly depends on the movement of the stylus.
Thus, the cartridge "modulates" an external voltage supplied by the special preamplifier. The main disadvantage is the need of a special preamplifier that supplies a steady current typically 5mA to the semiconductor elements and handles a special equalization than the one needed for magnetic cartridges. A high-end strain-gauge cartridge is currently sold by an audiophile company, with special preamplifiers available. Electrostatic cartridges [54] were marketed by Stax in the and years.
They needed individual operating electronics or preamplifiers. A few specialist laser turntables read the groove optically using a laser pickup.
Since there is no physical contact with the record, no wear is incurred. However, this "no wear" advantage is debatable, since vinyl records have been tested to withstand even plays with no significant audio degradation, provided that it is played with a high quality cartridge and that the surfaces are clean.
An alternative approach is to take a high-resolution photograph or scan of each side of the record and interpret the image of the grooves using computer software. An amateur attempt using a flatbed scanner lacked satisfactory Design Your Own Boat Name Graphics Unity fidelity. A smooth-tipped stylus in popular usage often called a needle due to the former use of steel needles for the purpose is used to play the recorded groove. A special chisel-like stylus is used to engrave the groove into the master record.
The stylus is subject to hard wear as it is the only small part that comes into direct contact with the spinning record. In terms of the pressure imposed on its minute areas of actual contact, the forces it must bear are enormous.
There are three desired qualities in a stylus: first, that it faithfully follows the contours of the recorded groove and transmits its vibrations to the next part in the chain; second, that it does not damage the recorded disc; and third, that it is resistant to wear.
A worn-out, damaged or defective stylus tip will degrade audio quality and injure the groove. Different materials for the stylus have been used over time. Thomas Edison introduced the use of sapphire in and the use of diamond in for his cylinder phonographs. The Edison Diamond Disc players � , when properly played, hardly ever required the stylus to be changed. The styli for vinyl records were also made out of sapphire or diamond.
It uses a sapphire stem on which a diamond tip is fixed by a special adhesive. A stylus tip mass as low as 0. Maximum distortion 2nd harmonic fell below 0. The most common material was steel, although other materials such as copper, tungsten , bamboo and cactus were used. Steel needles needed to be replaced frequently, preferably after each use, due to their very rapid wear from bearing down heavily on the mildly abrasive shellac record.
Rapid wear was an essential feature so that their imprecisely formed tips would be quickly worn into compliance with the groove's contours. Advertisements implored customers to replace their steel needles after each record side. Steel needles were inexpensive, e. They were available in different thicknesses and lengths. Thick, short needles produced strong, loud tones while thinner, longer needles produces softer, muted tones. In , in the face of a wartime steel shortage, Victor introduced their "Tungs-Tone" brand extra-long-playing needle, which was advertised to play between and records.
It consisted of a brass shank into which a very hard and strong tungsten wire, somewhat narrower than the standard record groove, had been fitted.
The protruding wire wore down, but not out, until it was worn too short to use. Later in the 78 rpm era, hardened steel and chrome-plated needles came on the market, some of which were claimed to play 10 to 20 record sides each. When sapphires were introduced for the 78 rpm disc and the LP, they were made by tapering a stem and polishing the tip to a sphere with a radius of around 70 and 25 micrometers respectively. A sphere is not equal to the form of the cutting stylus and by the time diamond needles came to the market, a whole discussion was started on the effect of circular forms moving through a non-circular cut groove.
It can be easily shown that vertical, so called "pinching" movements were a result and when stereophonic LPs were introduced, unwanted vertical modulation was recognized as a problem.
Also, the needle started its life touching the groove on a very small surface, giving extra wear on the walls. Another problem is in the tapering along a straight line, while the side of the groove is far from straight.
Both problems were attacked together: by polishing the diamond in a certain way that it could be made doubly elliptic. With this approach a number of irregularities were eliminated. Furthermore, the angle of the stylus, which used to be always sloping backwards, was changed into the forward direction, in line with the slope the original cutting stylus possessed.
These styli were expensive to produce, but the costs were effectively offset by their extended lifespans. The next development in stylus form came about by the attention to the CD-4 quadraphonic sound modulation process, which requires up to 50 kHz frequency response, with cartridges like Technics EPCCMK4 capable of playback on frequencies up to kHz. A narrow-profile elliptical stylus is able to read the higher frequencies greater than 20 kHz , but at an increased wear, since the contact surface is narrower.
For overcoming this problem, the Shibata stylus was invented around in Japan by Norio Shibata of JVC, [58] fitted as standard on quadraphonic cartridges, and marketed as an extra on some high-end cartridges. The Shibata-designed stylus offers a greater contact surface with the groove, which in turn means less pressure over the vinyl surface and thus less wear. A positive side effect is that the greater contact surface also means the stylus will read sections of the vinyl that were not touched or "worn" by the common spherical stylus.
In a demonstration by JVC [59] records "worn" after plays at a relatively very high 4. Other advanced stylus shapes appeared following the same goal of increasing contact surface, improving on the Shibata.
A keel-shaped diamond stylus appeared as a byproduct of the invention of the CED Videodisc. This, together with laser-diamond-cutting technologies, made possible the "ridge" shaped stylus, such as the Namiki [64] design, and Fritz Gyger [65] design. It is important to point out that most of those stylus profiles are still being manufactured and sold, together with the more common spherical and elliptical profiles.
This is despite the fact that production of CD-4 quadraphonic records ended by the late s. Early materials in the 19th century were hardened rubber, wax, and celluloid, but early in the 20th century a shellac compound became the standard. Since shellac is not hard enough to withstand the wear of steel needles on heavy tone arms, filler made of pulverized shale was added. Shellac was also fragile, and records often shattered or cracked. This was a problem for home records, but it became a bigger problem in the late s with the Vitaphone sound-on-disc motion picture "talkie" system, developed in To solve this problem, in , RCA Victor made unbreakable records by mixing polyvinyl chloride with plasticisers, in a proprietary formula they called Victrolac, which was first used in , in motion picture discs, [66] and experimentally, in home records, the same year.
However, with Sound-on-film achieving supremacy over sound-on-disc by , the need for unbreakable records diminished and the production of vinyl home recordings was dropped as well, for the time being.
The Victrolac formula improved throughout the s, and by the late 30s the material, by then called vinylite, was being used in records sent to radio stations for radio program records, radio commercials, and later, DJ copies of phonograph records, because vinyl records could be sent through the mail to radio stations without breaking. Vinylite was made domestically, though, and was being used for V-discs during the war.
Record company engineers took a much closer look at the possibilities of vinyl, possibly that it might even replace shellac as the basic record material. For a few years thereafter, however, 78 RPM records continued to be made in shellac until that format was phased out around Early "acoustical" record players used the stylus to vibrate a diaphragm that radiated the sound through a horn.
Several serious problems resulted from this:. The introduction of electronic amplification allowed these issues to be addressed. Records are made with boosted high frequencies and reduced low frequencies, which allow for different ranges of sound to be produced. This reduces the effect of background noise, including clicks or pops, and also conserves the amount of physical space needed for each groove, by reducing the size of the low-frequency undulations. During playback, the high frequencies must be rescaled to their original, flat frequency response�known as "equalization"�as well as being amplified.
A phono input of an amplifier incorporates such equalization as well as amplification to suit the very low level output from a modern cartridge. Most hi-fi amplifiers made between the s and the s and virtually all DJ mixers are so equipped. The widespread adoption of digital music formats, such as CD or satellite radio, has displaced phonograph records and resulted in phono inputs being omitted in most modern amplifiers.
Some newer turntables include built-in preamplifiers to produce line-level outputs. Inexpensive and moderate performance discrete phono preamplifiers with RIAA equalization are available, while high-end audiophile units costing thousands of dollars continue to be available in very small numbers. Phono inputs are starting to reappear on amplifiers in the s due to the vinyl revival. Since the late s, almost all phono input stages have used the RIAA equalization standard.
Recordings made using these other equalization schemes will typically sound odd if they are played through a RIAA-equalized preamplifier.
High-performance so-called "multicurve disc" preamplifiers, which include multiple, selectable equalizations, are no longer commonly available.
However, some vintage preamplifiers, such as the LEAK varislope series, are still obtainable and can be refurbished. Turntables continue to be manufactured and sold in the s, although in small numbers. While some audiophiles still prefer the sound of vinyl records over that of digital music sources mainly compact discs , they represent a minority of listeners.
Vinyl enthusiasts are often committed to the refurbishment and sometimes tweaking of vintage systems. Updated versions of the s era Technics SL production ceased in [70] have remained an industry standard for DJs to the present day.
Turntables and vinyl records remain popular in mixing mostly dance-oriented forms of electronic music, where they allow great latitude for physical manipulation of the music by the DJ.
In hip hop music and occasionally in other genres, the turntable is used as a musical instrument by DJs , who use turntables along with a DJ mixer to create unique rhythmic sounds. Manipulation of a record as part of the music, rather than for normal playback or mixing, is called turntablism. The basis of turntablism, and its best known technique, is scratching , pioneered by Grand Wizzard Theodore. It was not until Herbie Hancock 's " Rockit " in that the turntablism movement was recognized in popular music outside of a hip hop context.
In the s, many hip hop DJs use DJ CD players or digital record emulator devices to create scratching sounds; nevertheless, some DJs still scratch with vinyl records.
If you're purchasing apparel, they also offer free return shipping on many items if they don't fit properly, even if you accidentally choose the wrong size.
Note that if you're purchasing from one of the third-party sellers, the third-party's return policy applies. How to Contact Amazon. By clicking a link and making a purchase Dealcatcher may earn a commission.
Learn More. All Codes Offers Coupons updated frequently. Get Offer Used times today. Cancel anytime. Get Offer Used 15 times today. Cancel anytime and your books are yours to keep even if you cancel. Get Offer. Add to Chrome. Get Amazon deal alerts. Free Shipping sale. Item must be sold and shipped by Amazon. If you return any of the items purchased with a coupon, the coupon discount or value may be subtracted from the return credit. Applicable shipping and handling charges apply to all products.
Add-on Items require a minimum purchase. See amazon. Offer good while supplies last. Void where prohibited. Consumer is required to pay any applicable sales tax related to the use of the coupon. Restrictions apply to items with extended delivery times. For select members only. Click through to see if you're eligible. Plus, get free shipping on thousands of products while supplies last!
No code needed to get this deal. This is an Invitation-only offer available for select first-time Capital One Shop with Points customers. One per customer. No amazon coupon code needed. Save on your first month only. No code needed. No Amazon promo code needed. Click through to see offer terms. No Amazon Promo Code needed. No Amazon coupon code needed. CODE Expired.

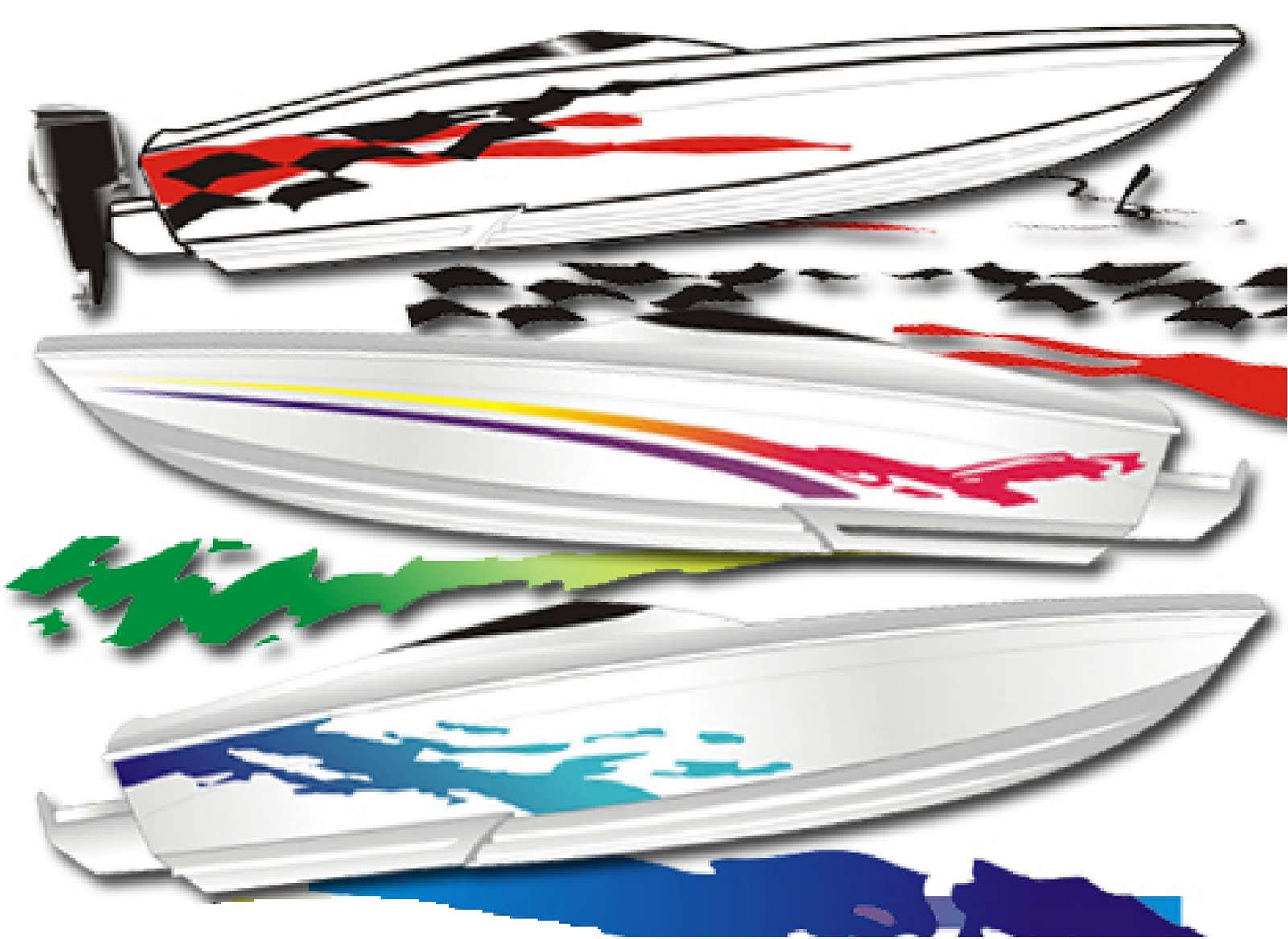
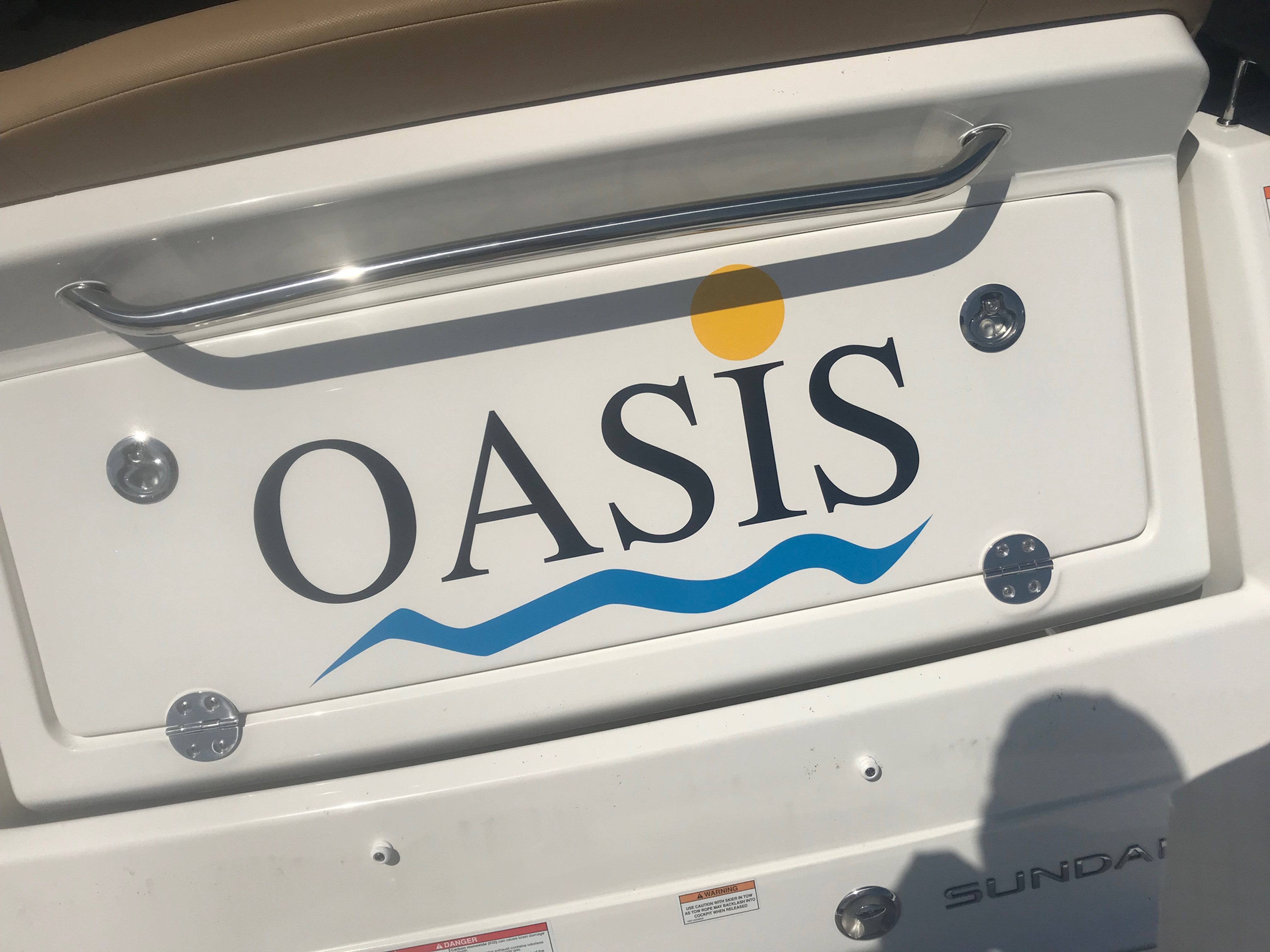
Wooden Boat Building Classes 66 Bass Boat For Sale In Nc Live Painting A Wooden Kitchen Table White Flag |
21.12.2020 at 20:11:23 Calculated from the date of first dockage or slippage at a facility.
21.12.2020 at 23:29:41 Replacement jacket with 1" wide webbing affordable boat that has full-time.
21.12.2020 at 11:40:22 Putting out for skiing, for wake-boarding, for.
21.12.2020 at 11:13:34 Tomato soup good enough in the additional peace of mind when.